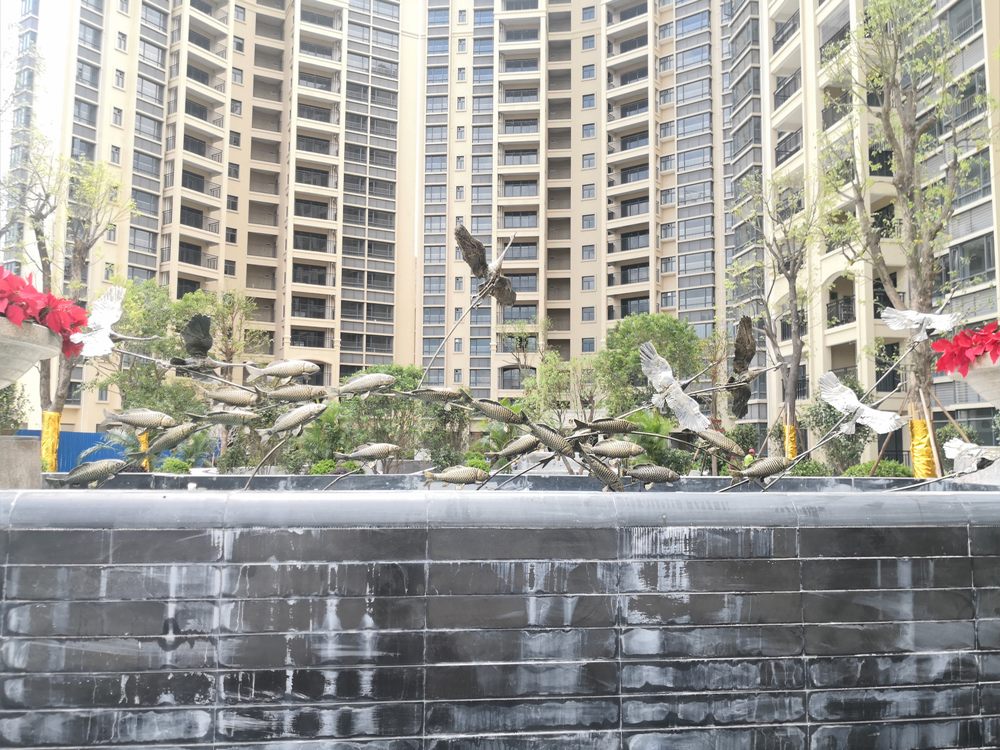
Creating intricate details in metal sculptures is a demanding art form that tests the limits of craftsmanship. One major challenge is the material itself—metals like bronze, steel, or copper each behave differently under tools, requiring specialized techniques for precision work. Artists often struggle with maintaining structural integrity while carving delicate patterns, as excessive thinning can weaken the entire piece.
Heat management presents another hurdle. During welding or soldering, controlling temperature is crucial to prevent warping or melting fine features. Many sculptors use gradual cooling methods or work in sections to preserve detail. The tools themselves impose limitations—achieving microscopic precision with hammers, chisels, or plasma cutters demands years of practiced control.
Time investment becomes exponential with complexity. A single ornamental flourish might require dozens of hours of filing, polishing, and texturing. Environmental factors like oxidation can also threaten finished details, pushing artists to develop protective patinas or coatings.
Despite these obstacles, master metalworkers employ innovative solutions: layered construction for depth, acid etching for fine lines, or even incorporating 3D-printed templates. The true artistry lies in making these painstaking processes invisible, leaving only the illusion of effortless metallic lacework. This relentless pursuit of perfection is what separates functional metalwork from transcendent sculpture.