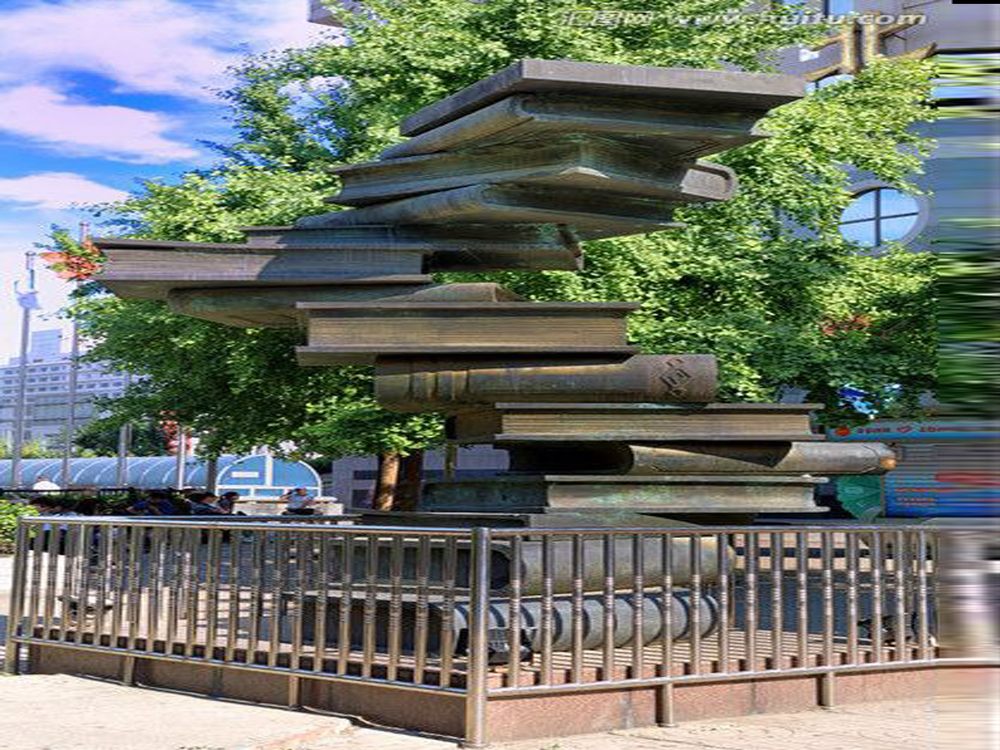
Sculptors often face the challenge of transporting large, intricate works to galleries, exhibitions, or public spaces. To overcome this, many adopt modular construction techniques, breaking down massive sculptures into smaller, manageable components. These modules are designed to fit together seamlessly, allowing for easy disassembly and reassembly without compromising the artwork’s integrity.
Modular construction not only simplifies logistics but also reduces costs associated with specialized transport and handling. For instance, heavy or oversized sculptures can be divided into lightweight sections, making them easier to move using standard vehicles. Additionally, this approach offers flexibility—artists can modify or expand their works by adding or reconfiguring modules.
Materials like fiberglass, aluminum, or 3D-printed parts are commonly used due to their durability and ease of assembly. Some sculptors even incorporate interlocking mechanisms or numbered guides to ensure precise reconstruction. This method is particularly popular for public art installations, where on-site assembly is often required.
By embracing modularity, sculptors balance artistic vision with practicality, ensuring their creations reach audiences worldwide without logistical hurdles.