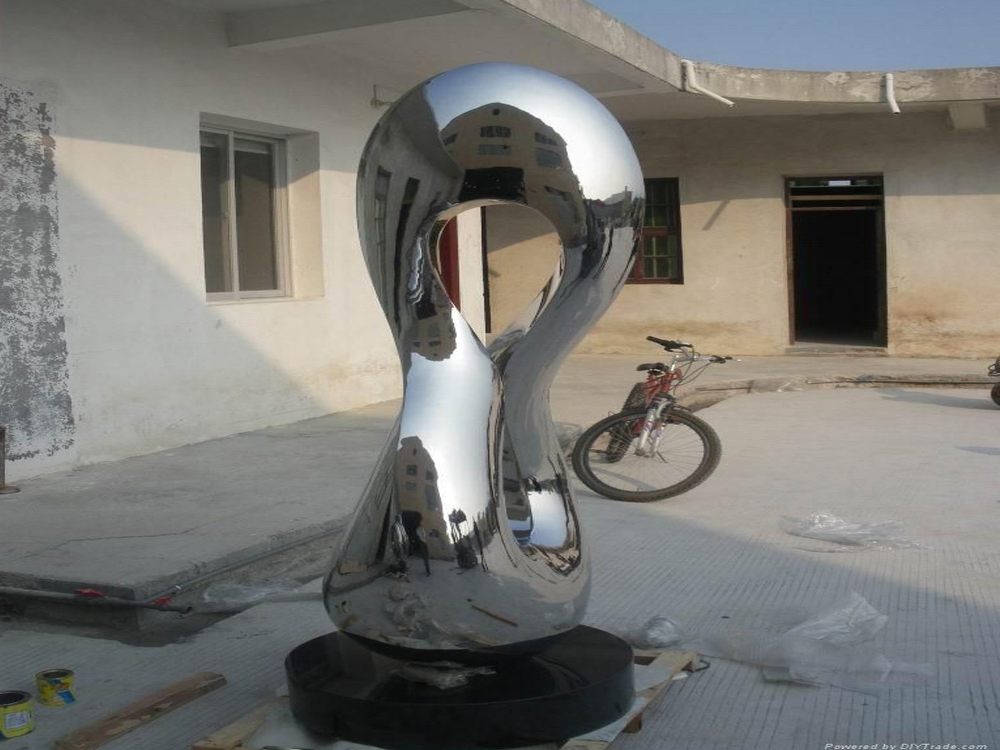
Welding dissimilar metals for sculptures presents unique challenges that require careful consideration and specialized techniques. One of the primary issues is metal compatibility, as different metals have varying melting points, thermal conductivities, and chemical properties. This incompatibility can lead to weak joints, cracks, or corrosion over time.
Thermal expansion is another significant challenge. Dissimilar metals expand and contract at different rates when heated, causing stress and distortion in the sculpture. To mitigate this, welders must carefully control heat input and use preheating or post-weld heat treatment techniques.
Additionally, the formation of brittle intermetallic compounds can weaken the weld joint. Choosing the right filler material and welding method, such as TIG or MIG welding, is crucial to ensure a strong bond. Proper surface preparation, including cleaning and removing oxides, is also essential to avoid contamination.
Finally, aesthetic considerations play a role in sculpture welding. The weld must not only be structurally sound but also visually appealing, blending seamlessly with the artwork. Mastering these challenges requires experience, patience, and a deep understanding of metallurgy and welding techniques.