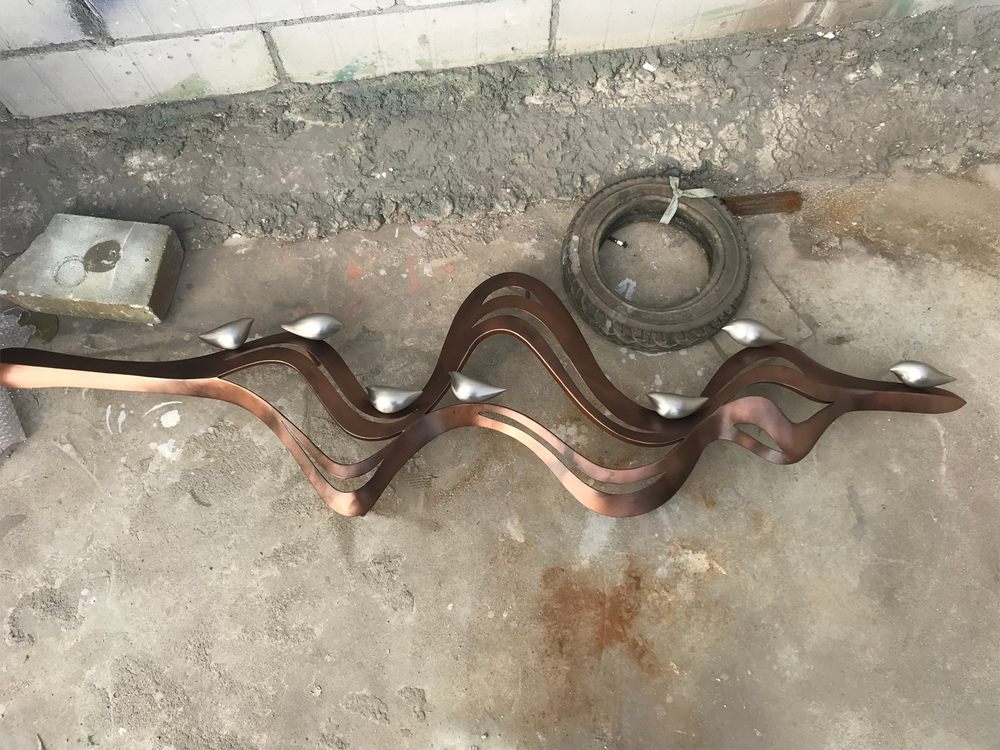
Collaborating with foundries for metal casting can be a complex process fraught with challenges that impact production timelines, costs, and final product quality. One of the most common issues is inconsistent material quality, where variations in raw metals or alloys lead to defects like porosity or cracks in castings. Foundries may also struggle with production delays due to equipment breakdowns, labor shortages, or inefficient scheduling, causing ripple effects across supply chains.
Communication gaps between manufacturers and foundries often exacerbate these problems, especially when technical specifications or design tolerances are unclear. Additionally, maintaining strict quality control standards can be difficult, as foundries may lack advanced inspection tools or standardized testing protocols. Environmental regulations and sustainability requirements further complicate collaborations, as foundries must balance compliance with cost-efficiency.
To mitigate these challenges, companies should establish clear contracts with detailed quality benchmarks, invest in joint training programs, and leverage digital tools for real-time monitoring. Building long-term partnerships with reliable foundries and conducting regular audits can also ensure smoother collaborations and higher-quality outcomes.