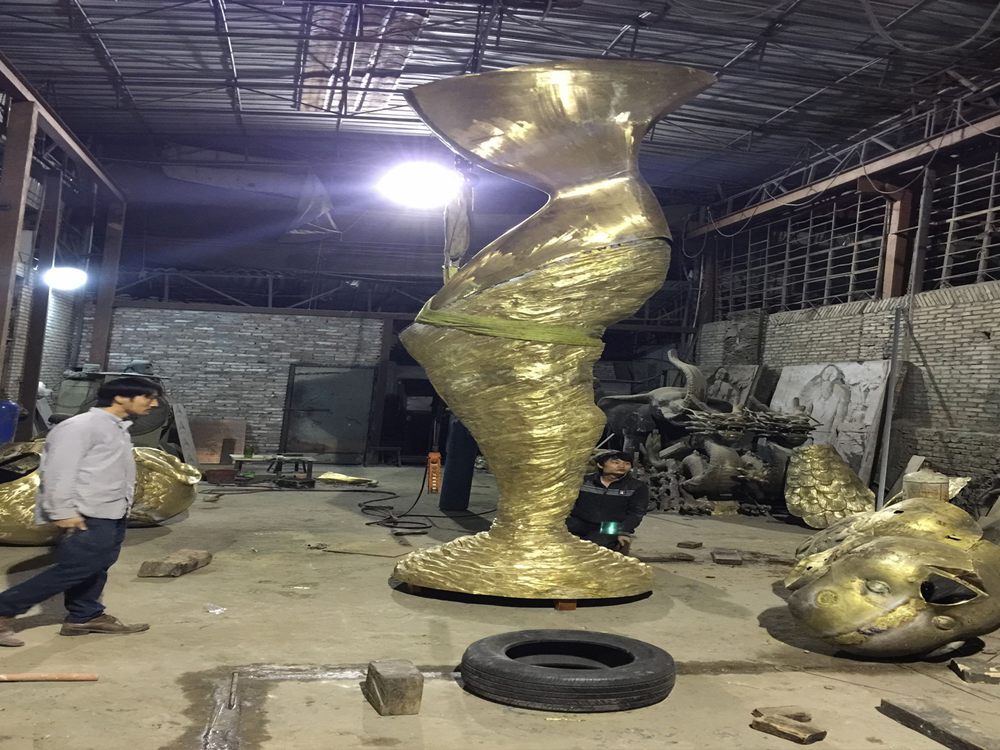
Creating kinetic metal sculptures that move with wind or motors is a fascinating yet complex art form that blends engineering and aesthetics. Artists and designers face several challenges in bringing these dynamic pieces to life.
1. Material Durability: Metal must withstand constant movement and environmental factors like wind, rain, and temperature changes. Choosing the right alloy—such as stainless steel or aluminum—is critical to prevent rust and fatigue over time.
2. Balancing Aesthetics and Function: The sculpture must look striking while ensuring its moving parts function smoothly. Overly intricate designs may hinder motion, while overly simplistic ones may lack visual appeal.
3. Mechanical Precision: For motorized sculptures, gears, motors, and bearings must be meticulously calibrated to avoid jerky or uneven movement. Wind-powered designs require careful weight distribution to respond naturally to breezes.
4. Structural Integrity: The sculpture’s base must support its weight and movement without tipping. Engineers often use counterweights or reinforced foundations to maintain stability.
5. Environmental Adaptation: Outdoor sculptures face unpredictable weather. Artists must account for wind speed variations, corrosion, and even bird interference, which can disrupt motion mechanisms.
6. Maintenance: Moving parts wear out. Regular lubrication, part replacements, and inspections are necessary to keep the sculpture operational, adding long-term costs.
Despite these challenges, kinetic metal sculptures captivate audiences with their fluid motion and innovative designs. By mastering these hurdles, artists create mesmerizing works that merge art and engineering in perfect harmony.