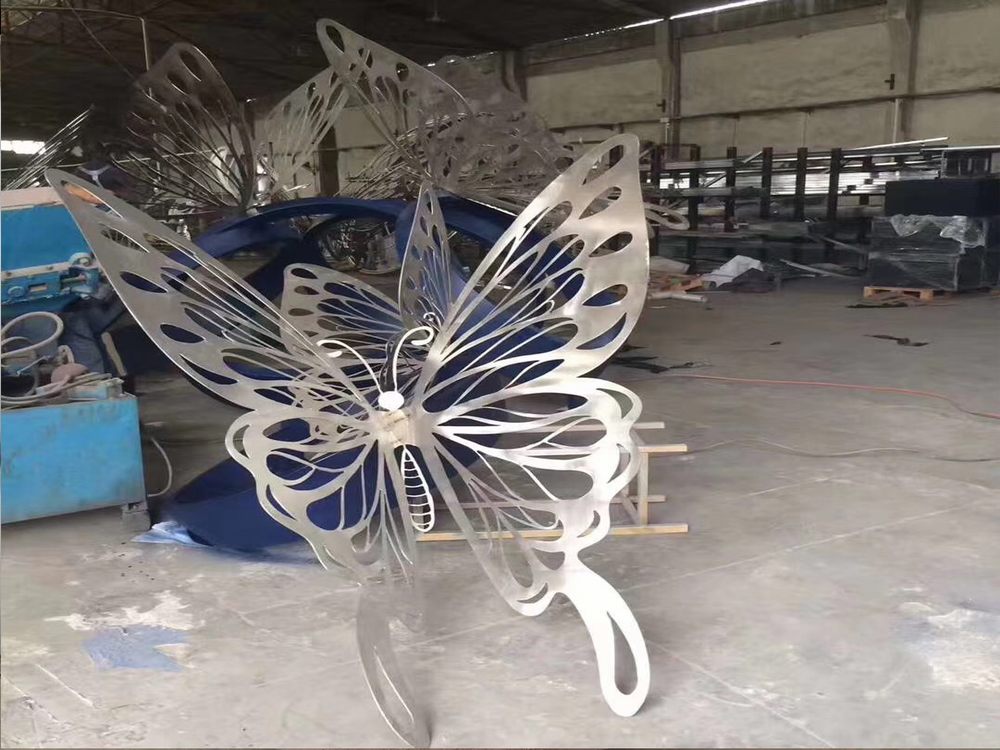
Preserving kinetic metal sculptures over extended periods presents a unique set of challenges that blend art conservation with mechanical engineering. Unlike static sculptures, these dynamic artworks face degradation from both environmental exposure and constant movement.
One major issue is material fatigue. The repetitive motion of kinetic sculptures stresses metal joints and components, leading to cracks or fractures over time. Stainless steel and aluminum are commonly used for their durability, but even these metals succumb to wear.
Corrosion poses another significant threat. Outdoor sculptures battle rust from rain, humidity, and pollution, while indoor pieces aren't immune to oxidation. Protective coatings require regular renewal, yet over-application can hinder movement.
Lubrication presents a paradox - necessary for smooth operation but potentially attracting dirt that accelerates wear. Conservators must find balance between functionality and preservation.
Perhaps most challenging is maintaining the artist's original kinetic intent. As components are replaced, the sculpture's movement characteristics may subtly change, potentially altering the artistic vision.
Modern conservation approaches combine traditional metalworking techniques with advanced materials science. Some institutions now use 3D scanning to document original movement patterns before restoration begins. Despite these advances, the preservation of kinetic metal sculptures remains an evolving field where art meets engineering in delicate balance.