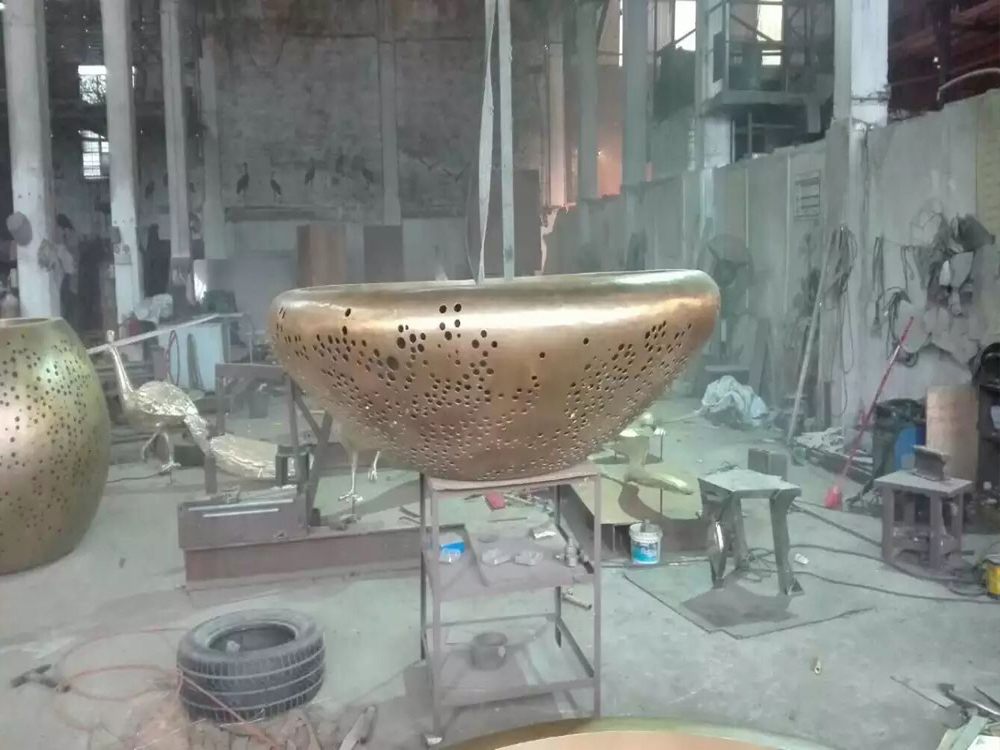
Metal fabrication serves vastly different purposes in industrial and artistic contexts, leading to distinct processes and outcomes. Industrial metal fabrication prioritizes efficiency, precision, and repeatability to meet standardized production demands. This sector relies heavily on automated machinery like CNC machines, laser cutters, and robotic welders to produce identical components at scale. Tolerances are measured in fractions of millimeters, with functionality taking precedence over aesthetics.
Artistic metal fabrication, conversely, celebrates uniqueness and creative expression. Artisans employ traditional techniques like hand-forging, repoussé, and custom welding to create one-of-a-kind pieces. While industrial fabrication uses primarily steel and aluminum, artists often incorporate precious metals, patinas, and mixed media. The artistic process values irregularity - hammer marks and weld lines frequently become intentional design elements rather than defects to eliminate.
Time considerations differ dramatically between the two approaches. Industrial projects operate on strict deadlines with optimized workflows, while artistic creations may involve months of experimentation. Cost structures also vary significantly, with industrial fabrication focusing on minimizing material waste and labor hours, whereas artistic works may justify higher costs through aesthetic value and craftsmanship.
Both disciplines require specialized skills, but with different emphases. Industrial fabricators master technical drawings and machinery operation, while artistic metalworkers develop skills in design principles and manual metal shaping techniques. Interestingly, some contemporary artists are bridging this divide by incorporating industrial methods into their creative process, demonstrating how these approaches can inform each other.