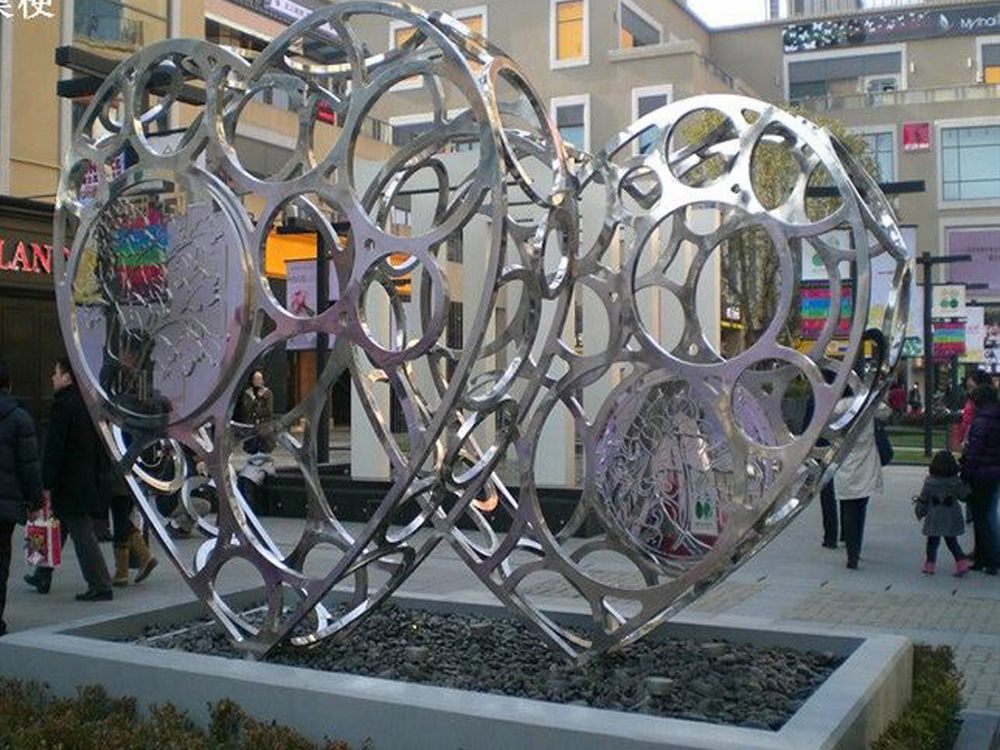
Creating sculptures that must be assembled on-site presents unique challenges that test both artistic vision and technical execution. One major hurdle is transportation logistics—large or complex pieces often require disassembly into smaller components, demanding precise engineering to ensure structural integrity upon reassembly.
Material selection becomes critical, as artists must balance durability with workability, especially when pieces will be exposed to environmental factors during transport and installation. Weight limitations for transport vehicles and crane capacities often dictate design adjustments, forcing artists to rethink traditional approaches.
The assembly process itself introduces coordination challenges, requiring clear instructions for installers who may lack the artist's intimate knowledge of the work. Weather conditions at the installation site can dramatically impact timelines and safety considerations, particularly for outdoor installations.
Fabrication tolerances prove especially demanding—components manufactured in different locations or at different times must fit together perfectly, requiring meticulous planning and often digital modeling. Budget constraints frequently compound these issues, as on-site assembly typically requires specialized labor and equipment.
Many artists address these challenges through modular designs, standardized connection systems, and thorough prototyping. Some incorporate the assembly process into the artistic concept itself, turning logistical necessities into aesthetic features. The most successful on-site sculptures emerge from artists who master both creative expression and practical problem-solving.