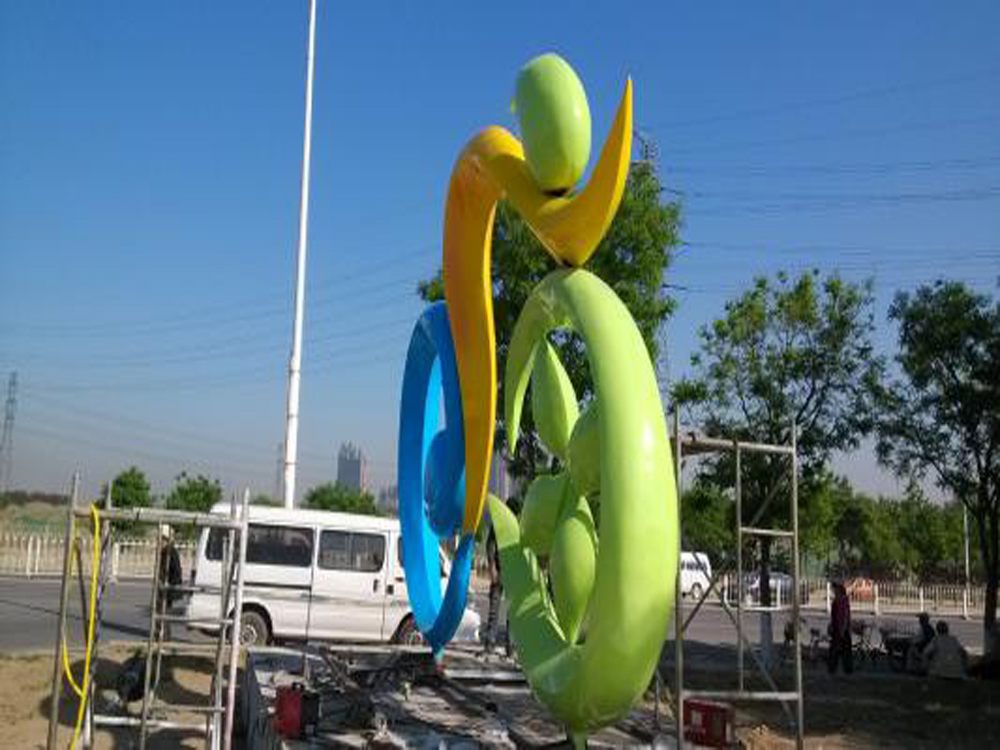
Creating complex metal sculptures often requires a seamless collaboration between artists, engineers, and fabricators. To ensure success, follow these best practices:
1. Clear Communication – From the outset, articulate your artistic vision with detailed sketches, 3D models, or digital renderings. Engineers and fabricators rely on precise instructions to translate creativity into structural integrity.
2. Early Involvement of Experts – Engage engineers and fabricators during the design phase. Their technical insights can prevent costly revisions and ensure feasibility, especially for large-scale or intricate pieces.
3. Material Selection Guidance – Fabricators can advise on the best metals (e.g., steel, bronze, aluminum) for durability, weight, and aesthetic finish, balancing artistic intent with practicality.
4. Prototyping and Testing – Develop small-scale prototypes to identify potential structural weaknesses or fabrication challenges before committing to the final piece.
5. Iterative Feedback Loops – Maintain open channels for feedback. Regular check-ins allow adjustments without derailing timelines or budgets.
6. Documentation and Tolerance Specifications – Provide exact measurements, weld details, and load-bearing requirements to avoid misinterpretations during fabrication.
7. Respect Technical Constraints – While creativity drives the project, acknowledge engineering limitations to ensure safety and longevity, especially for public installations.
By fostering mutual respect and leveraging each team member’s expertise, artists can achieve breathtaking metal sculptures that marry innovation with precision.