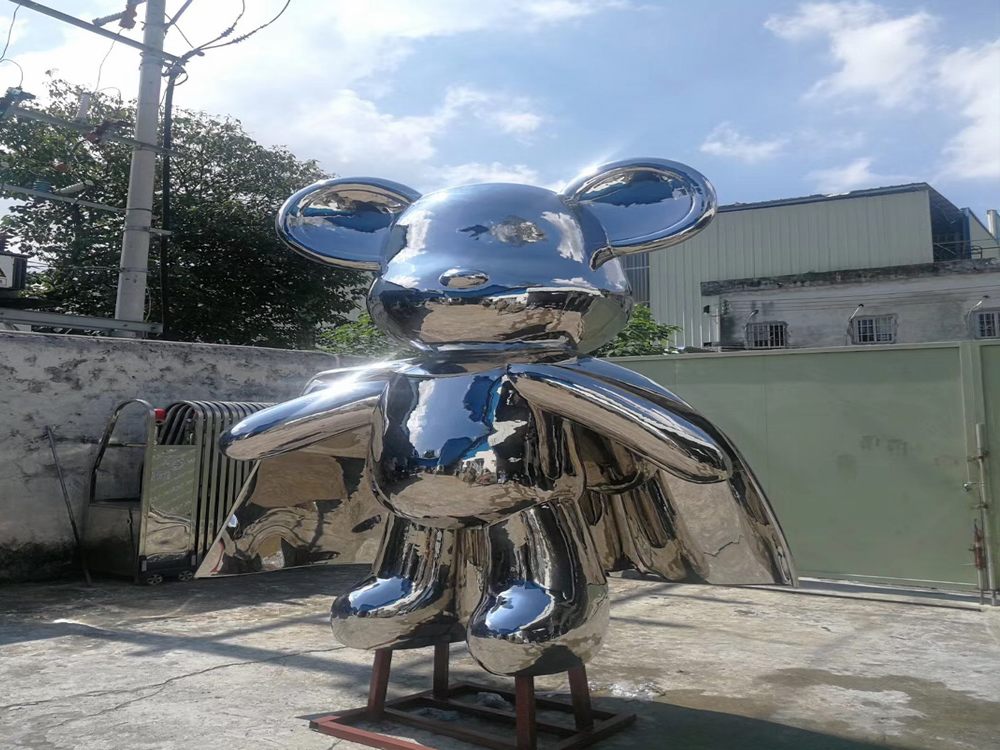
Sculptors often rely on scale models or maquettes as essential tools for planning large metal installations. These miniature versions allow artists to visualize the final piece, experiment with proportions, and identify potential structural challenges before committing to full-scale production.
The process begins with sketching and conceptualizing the design, followed by creating a detailed maquette from materials like clay, foam, or 3D-printed components. This model serves as a blueprint, helping sculptors refine details such as balance, weight distribution, and spatial relationships. For metal installations, factors like welding points and material stress are also tested at this stage.
Once the maquette is perfected, sculptors scale up the dimensions using precise measurements. Advanced techniques like 3D scanning or digital modeling may assist in translating the small-scale design into a larger format. This meticulous planning ensures the final metal installation aligns with the artist’s vision while maintaining structural integrity.
By using scale models, sculptors save time, reduce material waste, and achieve greater accuracy in their monumental works. This method bridges creativity and engineering, turning abstract ideas into tangible, awe-inspiring metal sculptures.