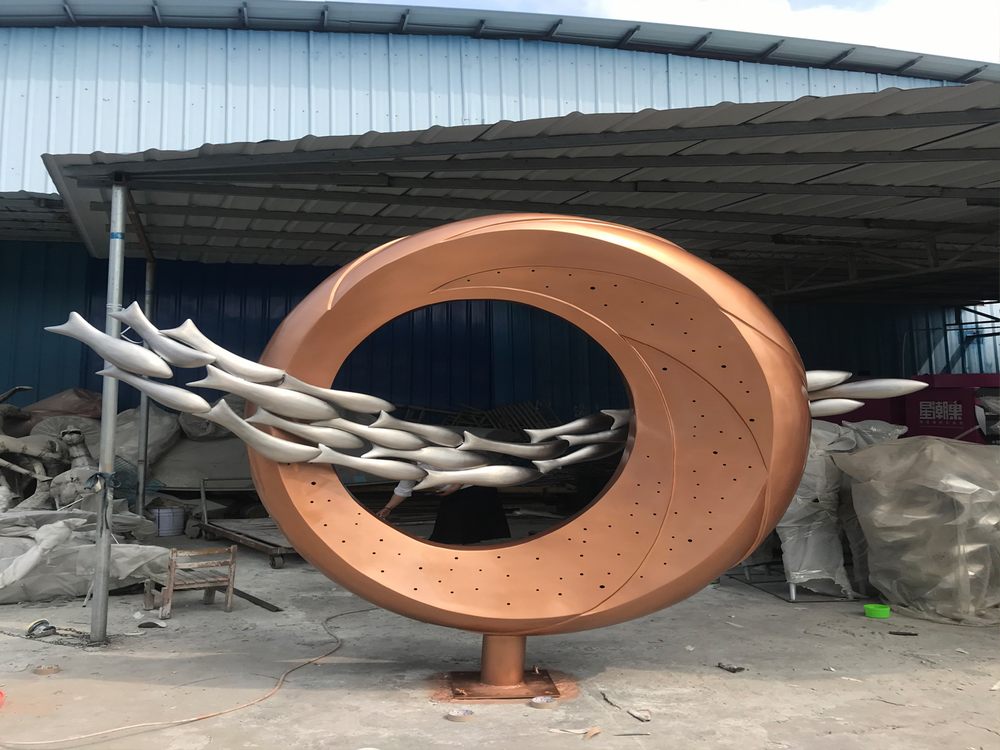
Collaborating with foundries for metal sculpture casting is a complex process that often presents several challenges for artists and creators. One of the most frequent issues is communication gaps between the artist and the foundry team. Misunderstandings about design intent, material choices, or finishing techniques can lead to costly revisions or unsatisfactory results.
Technical limitations also pose significant hurdles. Foundries may lack specialized equipment or expertise for highly intricate designs, forcing artists to compromise on their vision. Additionally, material inconsistencies, such as variations in metal alloys or impurities, can affect the final quality of the sculpture.
Budget constraints are another common challenge. Metal casting involves multiple steps—mold-making, pouring, finishing—each adding to the cost. Unexpected expenses, like additional patina work or structural reinforcements, can strain project budgets.
Timelines often become another pain point. Foundries juggle multiple projects, and delays in one phase can cascade, pushing delivery dates. Artists must factor in buffer time to accommodate these uncertainties.
Lastly, artistic integrity can be at risk. Some foundries prioritize efficiency over artistic nuance, potentially diluting the creator's original intent. Establishing clear expectations and maintaining open dialogue throughout the process is crucial for successful collaborations.
By understanding these challenges, artists can better prepare for foundry partnerships, ensuring smoother production and higher-quality results.