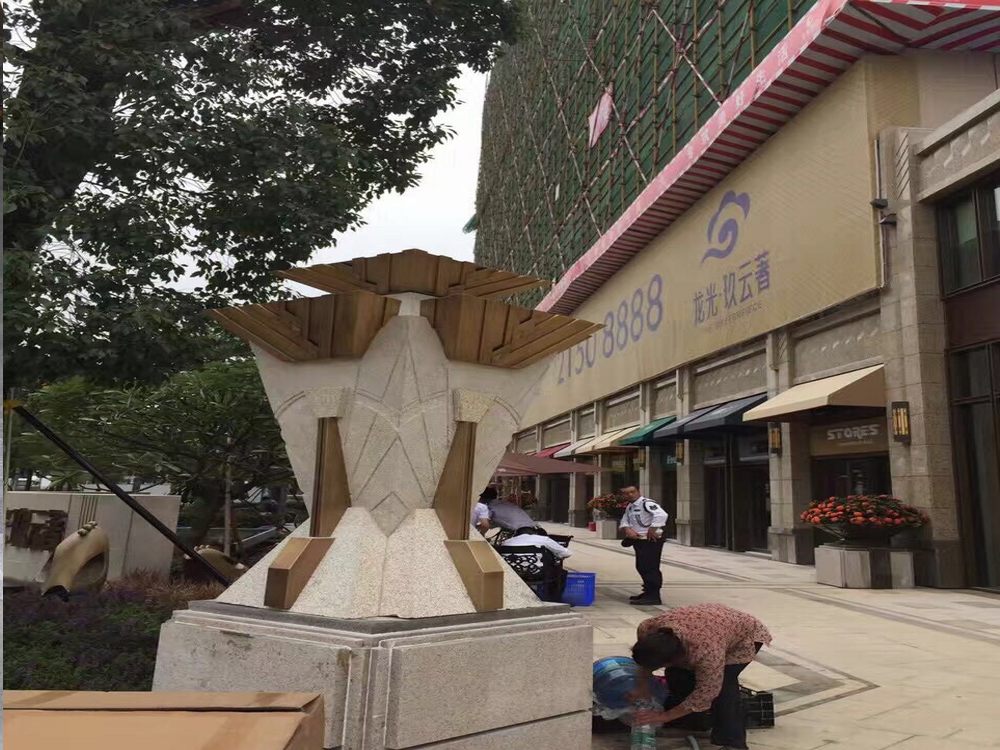
Creating a large bronze sculpture from a small maquette is a meticulous process that blends artistry with technical precision. Artists begin by refining their initial maquette, a small-scale model, to ensure every detail is perfected. Once satisfied, they employ methods like 3D scanning or manual measurement to scale up the design accurately.
For traditional enlargement, artists build an armature—a metal framework—that supports the sculpture’s weight and shape. Clay or wax is then applied to this structure, allowing the artist to refine the enlarged form. Modern techniques often involve 3D printing or CNC milling to create precise molds for larger versions.
The final step is bronze casting, typically using the lost-wax method. A mold is made from the scaled-up model, molten bronze is poured in, and after cooling, the sculpture is polished and patinated to achieve the desired finish. This intricate process ensures the artist’s original vision is preserved, even at a monumental scale.