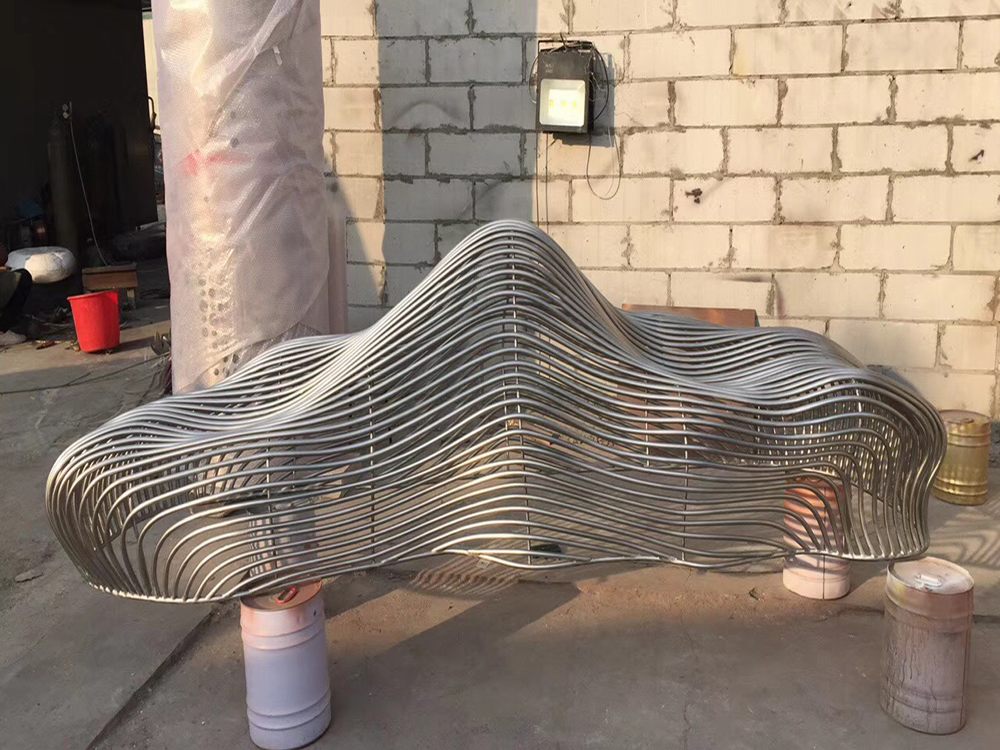
Creating multi-part bronze sculptures with seamless joins is a meticulous process that combines artistry and technical precision. Artists begin by designing the sculpture in sections, often using the lost-wax casting method to ensure each piece has clean edges. Once cast, the individual bronze components are carefully aligned and temporarily fixed using pins or clamps.
The key to invisible joins lies in skilled welding. Artists employ techniques like TIG (Tungsten Inert Gas) welding or brazing to fuse the pieces, followed by extensive chasing and repoussé work to blend the seams. Heat patination is then applied to unify the surface color and texture. Some sculptors even incorporate the joins into the artwork's design, turning structural necessities into aesthetic features.
Modern advancements like 3D scanning and digital modeling now help artists plan joins with millimeter accuracy before casting begins. The result is breathtaking bronze sculptures where the artist's hand remains invisible, letting the artwork speak as a unified whole.