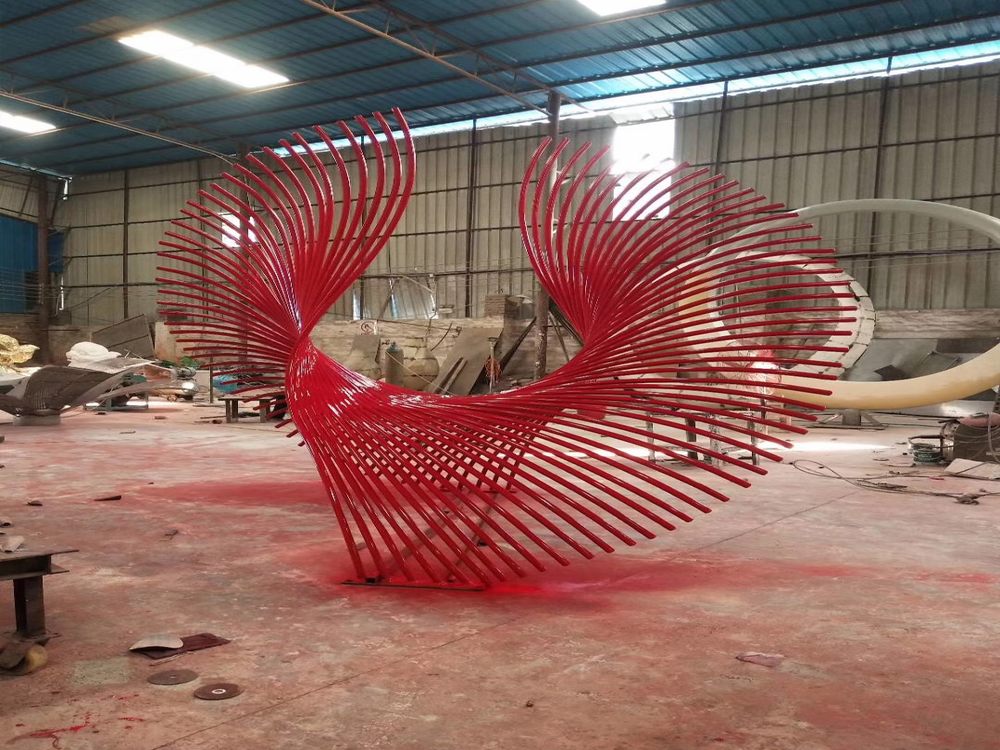
Creating hollow bronze sculptures is a delicate balance of artistry and engineering. Artists employ specialized techniques to achieve lightweight yet durable forms, primarily through the ancient lost-wax casting method. This process begins with a clay model that's coated in wax, then encased in a ceramic shell. When heated, the wax melts away (the "lost" wax), leaving a hollow mold for molten bronze.
Modern sculptors enhance structural integrity through several innovations:
1. Strategic wall thickness - Maintaining 1/4" to 1/2" bronze walls provides optimal strength-to-weight ratio
2. Internal armatures - Hidden steel frameworks support large or complex pieces
3. Modular casting - Large sculptures are cast in sections and expertly welded
4. Rib reinforcement - Internal bronze ribs add stability without visible exterior changes
Contemporary artists also use digital tools like 3D scanning to plan hollow sections precisely. The finished sculptures undergo meticulous chasing and patination, where surface treatments actually strengthen the metal. This combination of traditional craftsmanship and modern technology allows breathtaking bronze works to withstand centuries while appearing weightless and delicate.