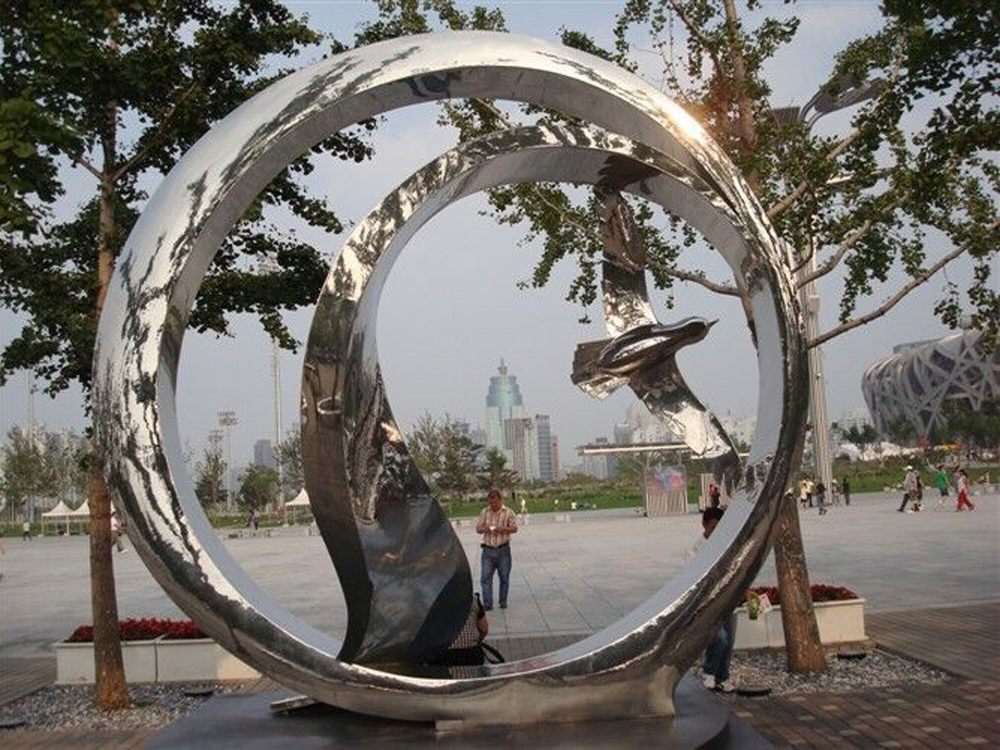
Cold casting and traditional bronze casting are two distinct methods used in sculpture and art reproduction, each with unique advantages and applications.
1. Materials Used
Cold casting involves mixing resin with metal powders (like bronze, copper, or aluminum) to create a metal-like finish without high-temperature processes. Traditional bronze casting, on the other hand, uses molten bronze poured into a mold, requiring extreme heat (over 1,000°C).
2. Process Complexity
Cold casting is simpler and safer, as it doesn’t require furnaces or specialized foundry equipment. Artists mix resin with metal powder, pour it into a mold, and let it cure. Bronze casting involves multiple steps: creating a wax model, building a ceramic shell, burning out the wax, and pouring molten metal—a labor-intensive and hazardous process.
3. Durability and Finish
Bronze castings are heavier, more durable, and can withstand outdoor conditions for centuries. Cold cast pieces are lighter and may degrade over time when exposed to UV rays or harsh weather, though they mimic the look of metal well.
4. Cost and Accessibility
Cold casting is cheaper and more accessible for small studios or hobbyists due to lower material and equipment costs. Traditional bronze casting is expensive, requiring skilled labor and specialized facilities.
5. Artistic Applications
Bronze casting is favored for high-end sculptures and public monuments. Cold casting is ideal for reproductions, decorative items, and prototypes where cost and ease of production are priorities.
In summary, cold casting offers affordability and simplicity, while bronze casting delivers unmatched durability and prestige. The choice depends on the project’s needs, budget, and intended longevity.