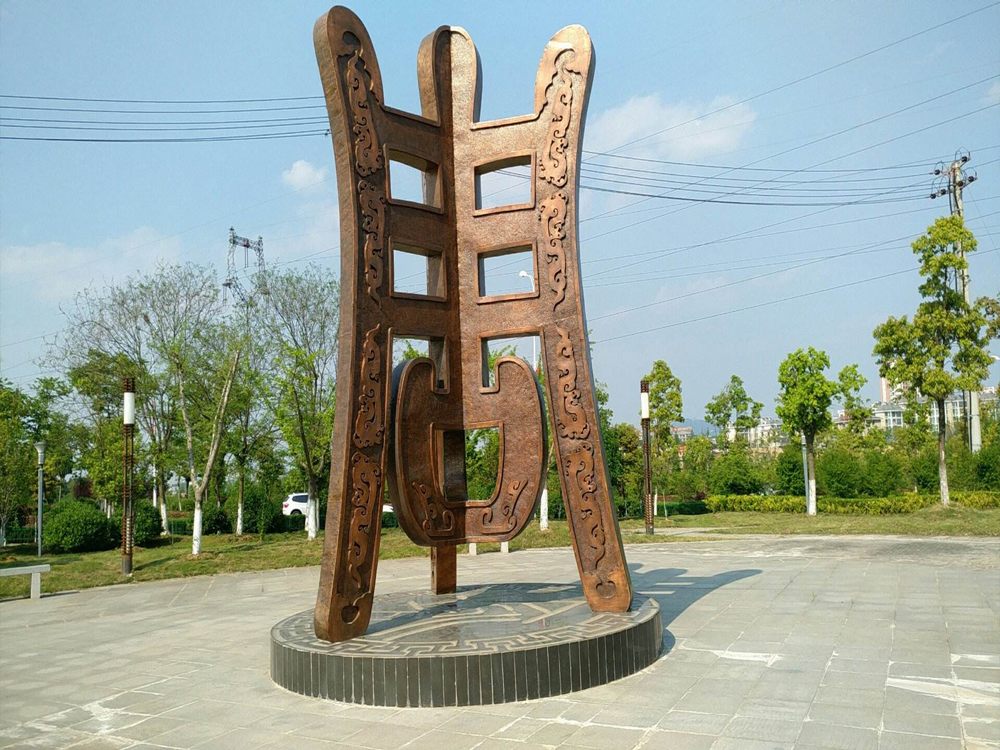
Wood carvers employ several techniques to ensure consistency when producing multiple copies of the same design. One of the most effective methods is using templates or stencils, which serve as precise guides for each carving. These templates are often made from durable materials like metal or hard plastic to withstand repeated use.
Another key technique involves meticulous measurement and marking. Carvers use calipers, rulers, and marking gauges to ensure every dimension matches the original design. Some artisans even create jigs or custom holding devices to maintain uniformity during the carving process.
Experienced carvers also develop muscle memory through practice, allowing them to replicate strokes and cuts with remarkable accuracy. For complex designs, many professionals work in stages, completing one specific detail across all pieces before moving to the next element.
Modern carvers sometimes incorporate technology, using CNC machines or laser guides for particularly intricate or large production runs. However, even with these tools, the artisan's eye for detail remains crucial in maintaining the handmade quality while achieving consistency across multiple pieces.
The finishing process also plays a vital role in creating uniform appearances. Carvers apply stains, paints, or sealants in controlled environments to ensure each piece receives identical treatment, resulting in a cohesive collection of carvings.