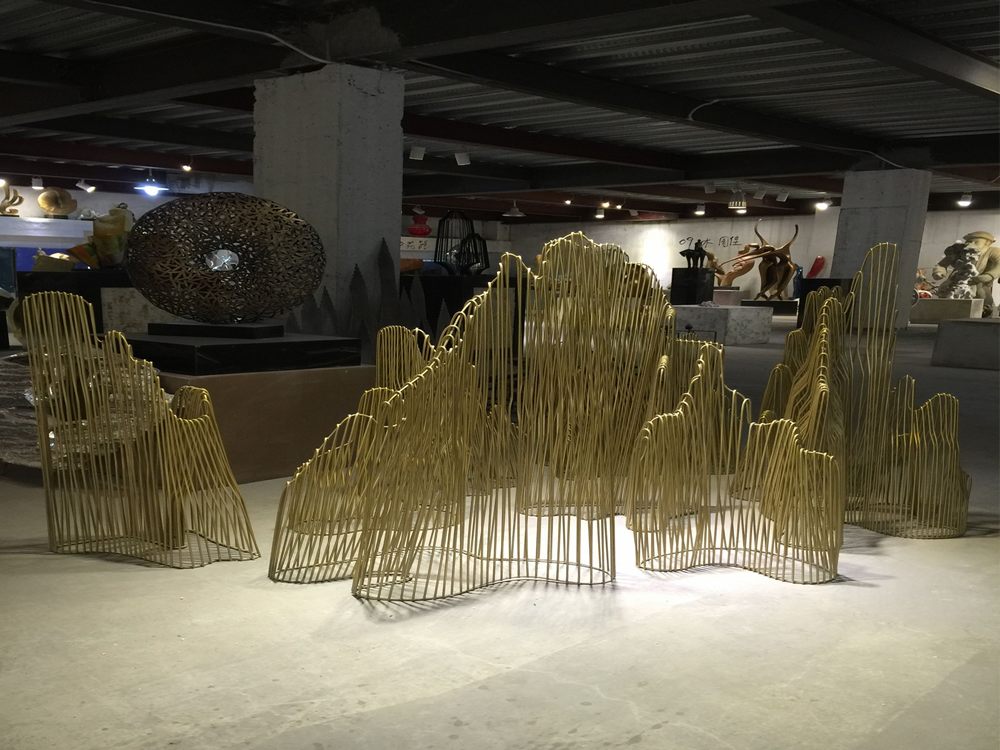
Wood carvings, a centuries-old art form, are embracing the digital age through techniques like 3D printing. This adaptation bridges the gap between traditional craftsmanship and modern fabrication, offering new possibilities for artists and designers.
One key advantage is precision. Digital tools allow intricate designs to be replicated with accuracy, preserving the authenticity of hand-carved details while reducing human error. Artists can scan original wood carvings and refine them digitally before 3D printing, ensuring consistency in mass production.
Material innovation also plays a role. While traditional wood remains popular, 3D printing enables experimentation with composite materials that mimic wood’s texture and grain. This expands creative options without sacrificing the aesthetic appeal of natural wood.
Moreover, digital fabrication democratizes access. Aspiring sculptors can now learn and practice using 3D models before transitioning to physical carving, lowering barriers to entry. Workshops and online platforms further facilitate this blend of old and new techniques.
Despite these advancements, purists argue that the tactile essence of hand-carving cannot be replaced. Yet, the synergy of digital and traditional methods fosters innovation, ensuring wood carving’s relevance in contemporary art and design.
By integrating 3D printing, wood carvings evolve—honoring heritage while embracing the future. This fusion not only preserves cultural artistry but also opens doors to unprecedented creative expression.