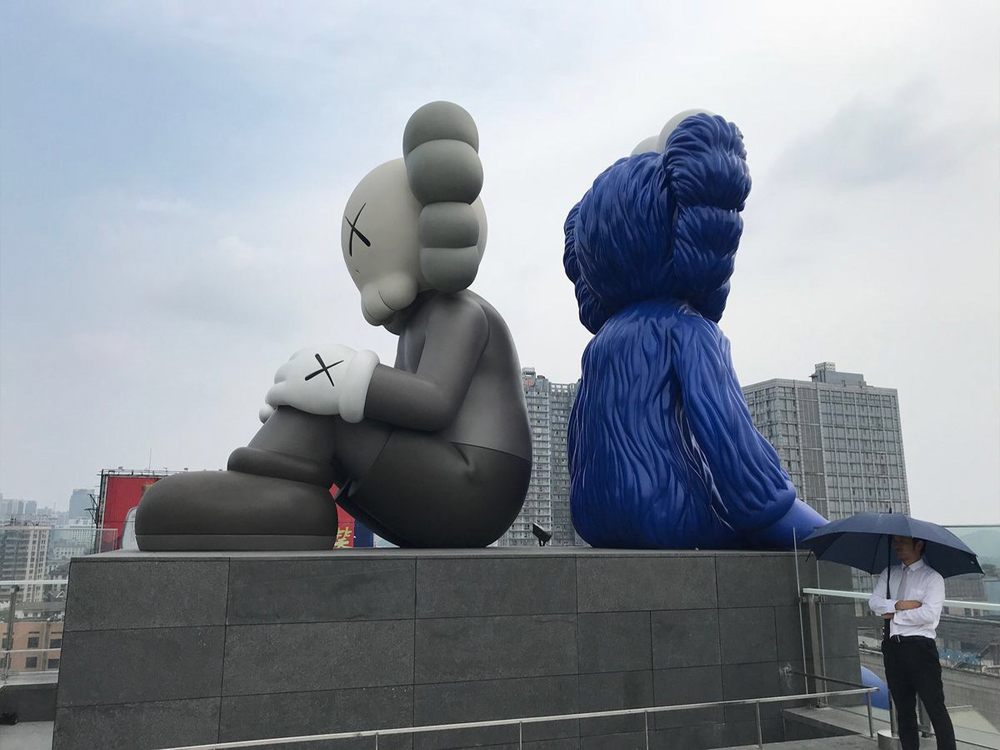
Porcelain sculptures are prized for their delicate beauty, but even the finest pieces can develop defects during production. The most common flaws include cracks, warping, glaze imperfections, air bubbles, and discoloration. Cracks often occur due to uneven drying or firing, while warping results from improper kiln temperatures. Glaze defects like pinholes or crawling happen when the coating fails to adhere properly.
Quality control teams use multiple methods to detect these issues. Visual inspection under bright light reveals surface flaws, while tap tests identify hidden cracks by sound resonance. Advanced workshops employ UV lights to spot glaze inconsistencies and magnification tools for micro-cracks. Some manufacturers even use X-ray scanning for structural integrity checks.
Prevention remains key – artisans control humidity during drying, monitor kiln temperatures precisely, and test glaze formulas thoroughly. When defects are found, pieces are either repaired (for minor issues) or discarded to maintain quality standards. Understanding these common problems helps collectors appreciate the skill required to create perfect porcelain artworks.