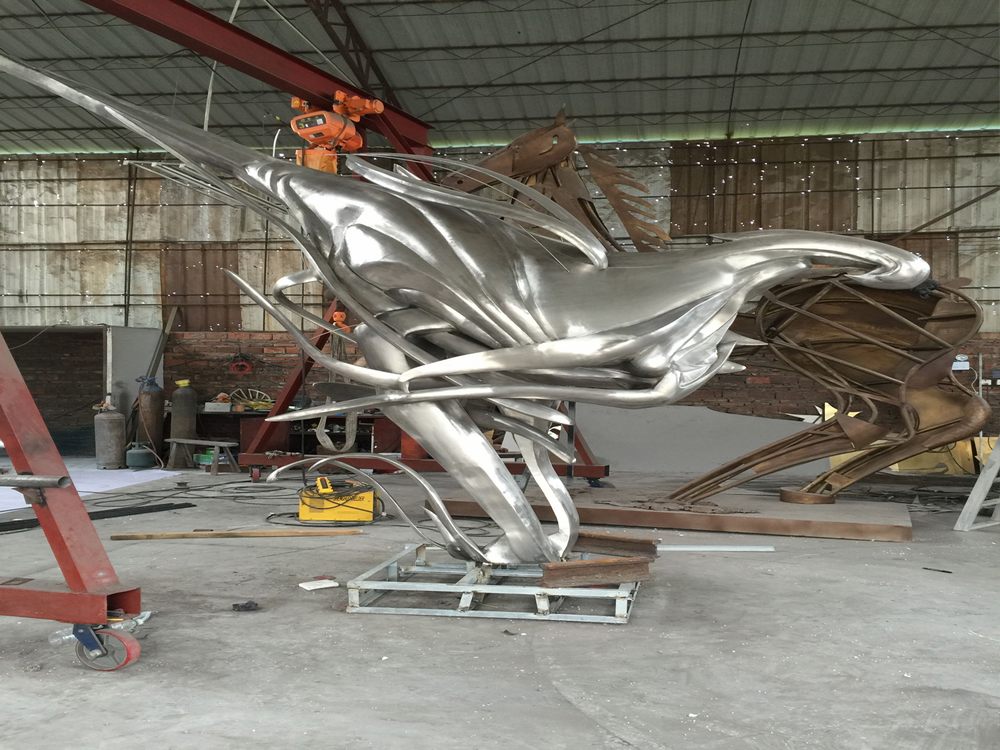
Creating porcelain sculptures with intricate pierced designs represents one of the most demanding disciplines in ceramic arts. Artists achieve this extraordinary level of detail through a combination of specialized techniques, exceptional patience, and generations of accumulated knowledge.
The process begins with preparing an exceptionally pure porcelain clay body, refined to remove all impurities that might weaken the delicate structures. Master sculptors work with custom-made tools - ultra-fine needles, miniature loop tools, and precision knives - often hand-forged to their exact specifications.
Before any piercing begins, the artist carefully plans the negative space patterns, sometimes creating paper templates or making pencil markings directly on the bisque-fired piece. The actual piercing occurs at the leather-hard stage, when the clay has just enough strength to hold its shape but remains soft enough to carve.
Artists employ various piercing methods:
1. Direct carving with fine blades for geometric patterns
2. Drill-assisted piercing for perfect circular openings
3. Water-jet technology in contemporary pieces
4. Traditional bamboo tools for organic designs
The most challenging aspect involves maintaining structural integrity while removing up to 70% of the material in some sections. Master artists develop an intuitive understanding of stress points, often leaving tiny "bridges" of clay between openings for support.
After piercing, the piece undergoes multiple firings, with special attention to kiln temperature ramping to prevent warping. Glazing presents another challenge - artists either carefully hand-paint each opening or use dipping techniques that leave the pierced sections unglazed for contrast.
This painstaking process, perfected over centuries in Chinese ceramic centers like Jingdezhen, continues to evolve as contemporary artists push the boundaries of what's possible in porcelain piercing art. The resulting sculptures stand as testaments to human patience, precision, and artistic vision.