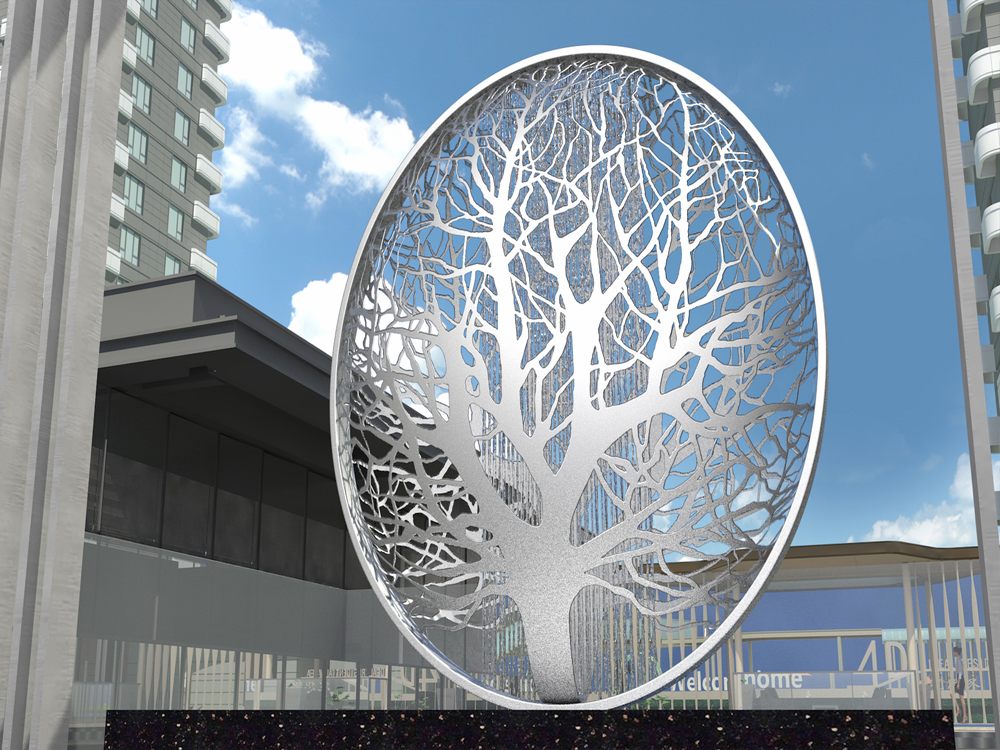
The durability and aesthetic finish of porcelain sculptures are profoundly influenced by the firing temperatures used during their creation. Porcelain, a high-fired ceramic material, undergoes significant physical and chemical transformations at different kiln temperatures, which ultimately determine its strength, porosity, and visual appeal.
Low-fire porcelain (around 1,000–1,150°C) produces sculptures with a softer, more porous structure. While this temperature range allows for vibrant glaze colors, the resulting pieces are less durable and more prone to chipping or cracking. Mid-range firing (1,150–1,250°C) strikes a balance, offering improved durability while retaining some of the glaze's brilliance.
High-fire porcelain (1,250–1,400°C) yields the most durable results. The extreme heat vitrifies the clay, creating a dense, glass-like structure that is highly resistant to wear and moisture. However, the higher temperatures can limit glaze options, often resulting in more subdued finishes.
The choice of firing temperature also affects the sculpture's final texture and sheen. Low-fire pieces tend to have a matte or satin finish, while high-fire sculptures exhibit a luminous, translucent quality prized in fine porcelain. Understanding these temperature effects allows artists to tailor their firing process to achieve the desired balance of strength and beauty in their ceramic creations.