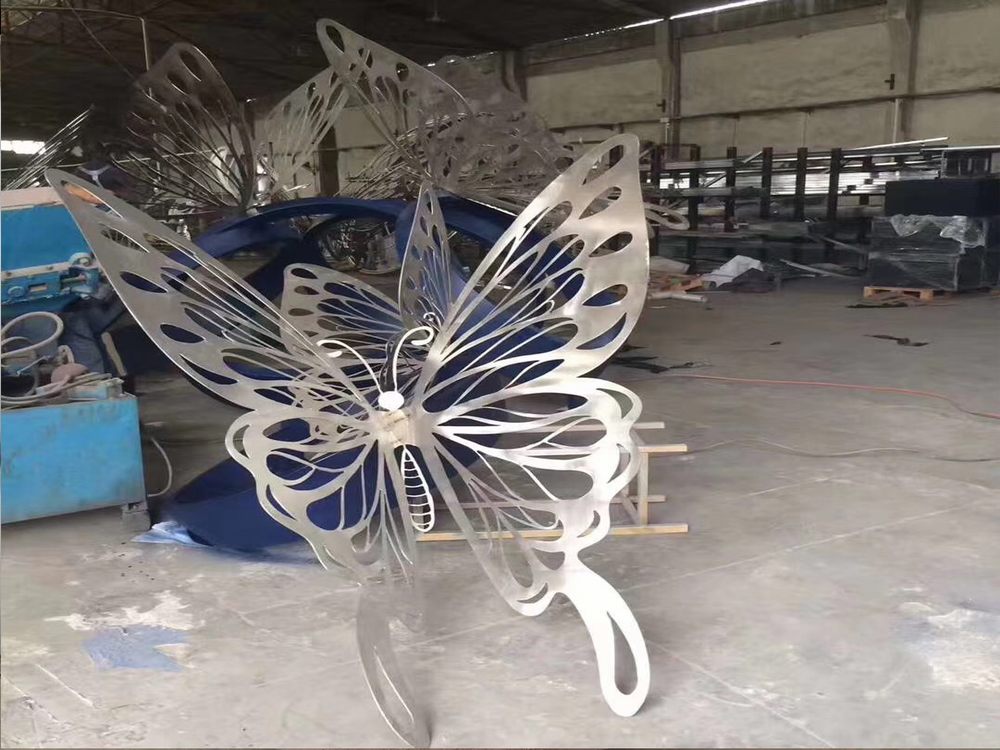
Creating geometric porcelain sculptures with high precision requires a blend of technical skill, patience, and innovative methods. Artists begin by selecting fine-grained porcelain clay, which allows for smoother shaping and sharper edges. The clay is carefully wedged to remove air bubbles, ensuring uniformity and reducing the risk of cracks during firing.
Precision is achieved through meticulous measuring and marking, often using calipers, templates, or 3D-printed guides to maintain exact proportions. Many artists employ slip-casting techniques for complex geometric forms, pouring liquid clay into precisely crafted molds. Hand-building methods, such as slab construction, require steady hands and repeated adjustments to align edges perfectly.
Firing plays a critical role—artists control kiln temperatures precisely to prevent warping while maintaining the sculpture’s structural integrity. Glazing is applied in thin, even layers to preserve crisp lines, sometimes using masking techniques to protect sharp angles.
Mastery of these techniques, combined with an artistic eye for symmetry and balance, allows ceramicists to produce stunning geometric porcelain works that captivate with their flawless precision.