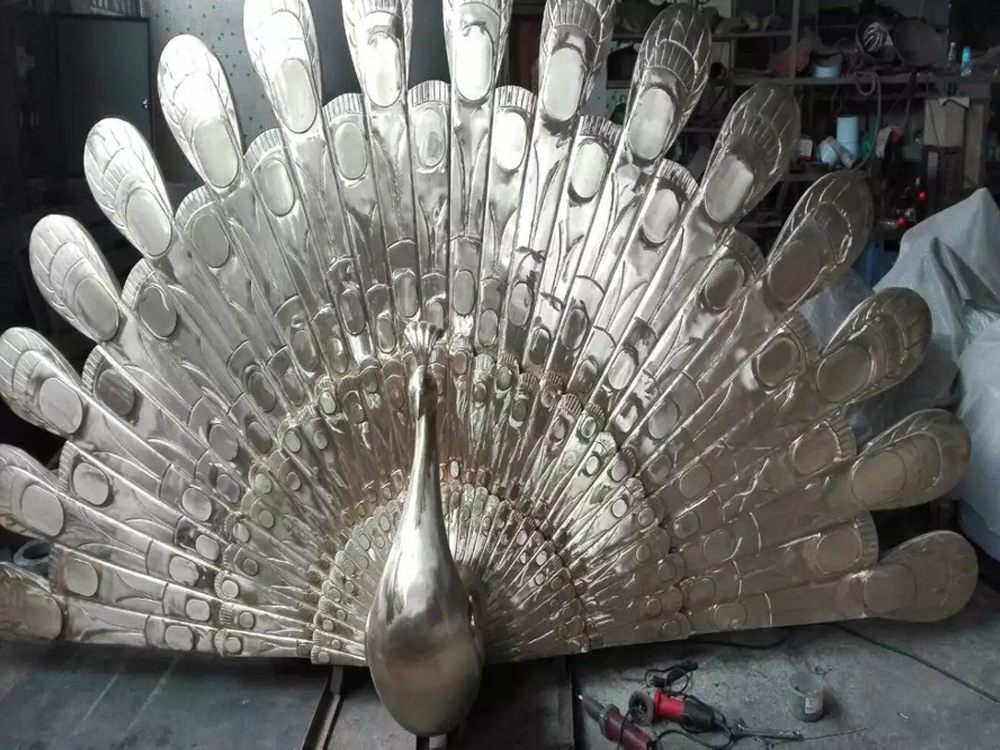
Porcelain sculptures are admired for their delicate beauty, but they are prone to several common defects that can compromise their appearance and longevity. Understanding these flaws and how to prevent them is essential for collectors and artists alike.
1. Cracks and Fissures: These often occur due to rapid temperature changes or improper drying. To avoid them, ensure slow, even drying before firing and use high-quality clay with balanced moisture content.
2. Glaze Defects (Crawling, Pinholes): Poor glaze application or contamination can cause uneven surfaces. Always clean bisque ware thoroughly and apply glaze in thin, even layers.
3. Warping: Uneven thickness or improper kiln placement leads to warping. Design sculptures with uniform thickness and use kiln stilts for even heat distribution.
4. Color Fading: Over-firing or low-quality pigments may cause colors to fade. Use stable underglazes and follow recommended firing temperatures.
5. Blisters and Bubbles: Trapped air or over-firing creates surface bubbles. Properly wedge clay and fire at correct temperatures to prevent this issue.
By following these best practices—meticulous material selection, controlled drying, and precise firing—artists can minimize defects and preserve the elegance of porcelain sculptures for generations. Regular inspection and gentle handling also play a crucial role in maintenance.