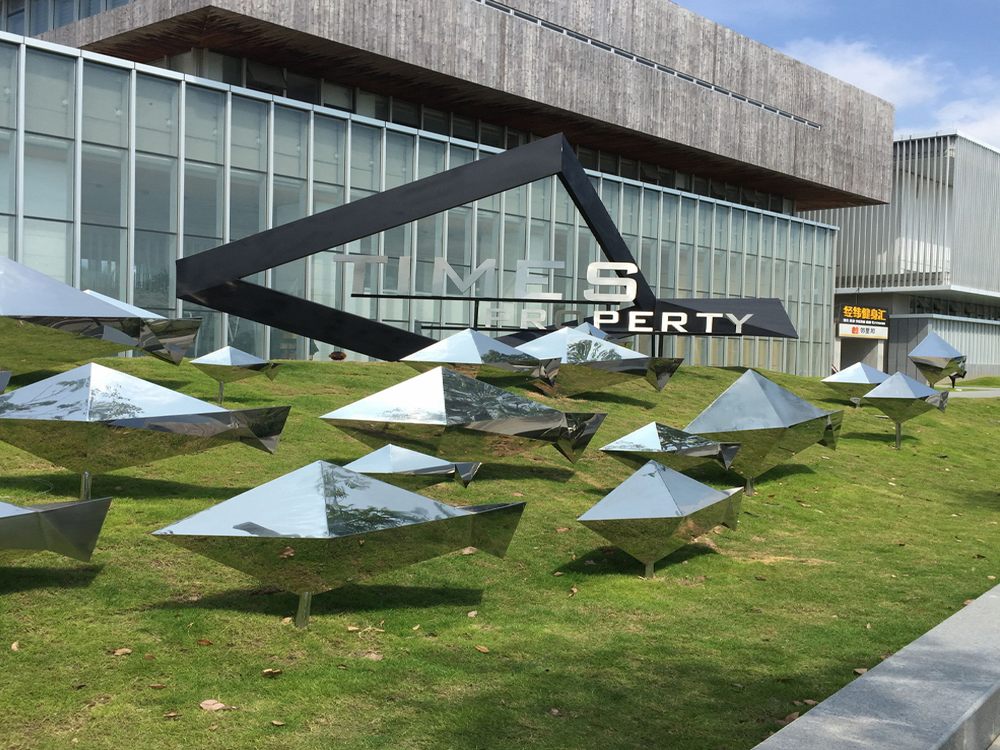
Creating porcelain sculptures with smooth, flawless surfaces and no visible seams is a testament to an artist's skill and attention to detail. The process begins with selecting high-quality porcelain clay, known for its fine texture and plasticity. Artists often use slip casting or hand-building techniques, ensuring each piece is molded with precision.
To eliminate seams, craftsmen meticulously join sections while the clay is still pliable, blending edges with specialized tools like ribs and sponges. After drying, the sculpture undergoes careful sanding to smooth any imperfections. Multiple firings at controlled temperatures strengthen the piece and prepare it for glazing.
Glazing plays a crucial role in achieving a seamless finish. Artists apply layers of glaze evenly, often using airbrushing or dipping methods, to create a uniform surface. The final firing melts the glaze into a glass-like coating, concealing any minor flaws.
Mastery of these techniques, combined with patience and artistic vision, allows porcelain sculptors to produce breathtaking works with immaculate, seamless surfaces.