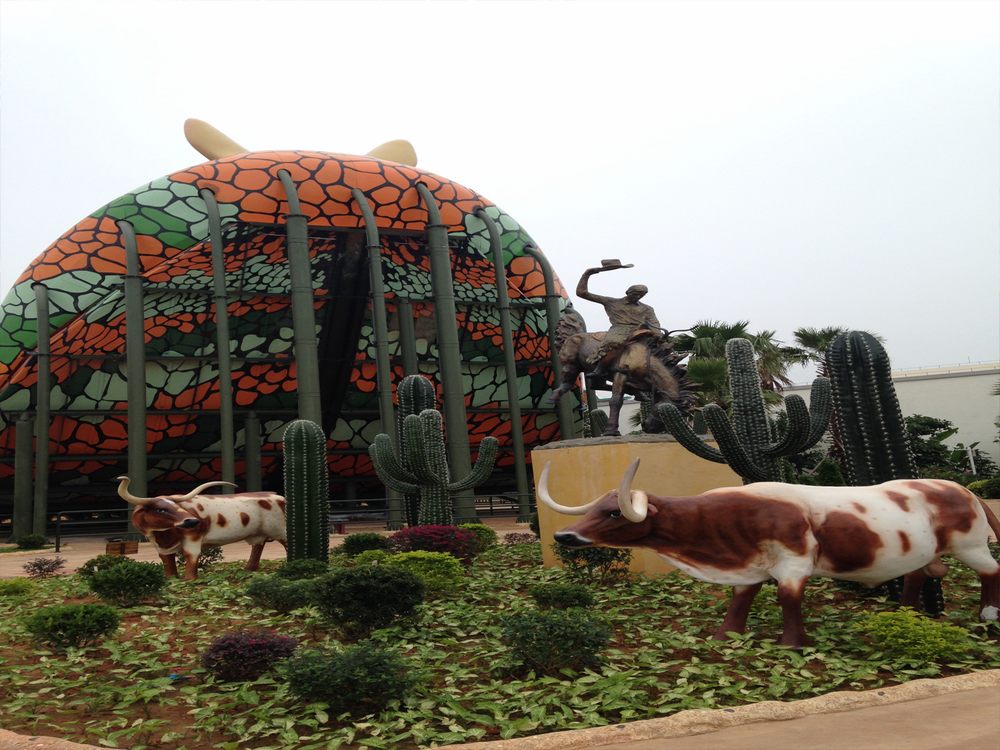
Creating large-scale porcelain sculptures presents unique artistic and technical hurdles that test even experienced ceramic artists. The inherent fragility of porcelain clay demands meticulous handling during construction, as the material becomes increasingly vulnerable as size increases. Structural integrity poses another major challenge - artists must engineer internal support systems while maintaining aesthetic purity, often using hidden armatures or strategic wall thickness variations.
Kiln firing introduces further complications. Large pieces risk cracking or warping due to uneven heat distribution, requiring carefully calibrated firing schedules that may span days. The weight of massive sculptures also strains kiln shelves, necessitating custom kiln designs or sectional firing approaches. Glazing at scale becomes exponentially difficult, as achieving consistent surface treatment requires innovative application methods beyond traditional brushing or dipping.
Transportation and installation of finished works present final obstacles. Porcelain's brittle nature makes moving multi-piece installations risky, often requiring specialized crating and on-site assembly. Despite these challenges, contemporary artists continue pushing boundaries by developing new techniques like slip-casting modular components or using hybrid materials that preserve porcelain's luminous quality while enhancing durability. The pursuit of monumental porcelain art remains a testament to human creativity overcoming material limitations.