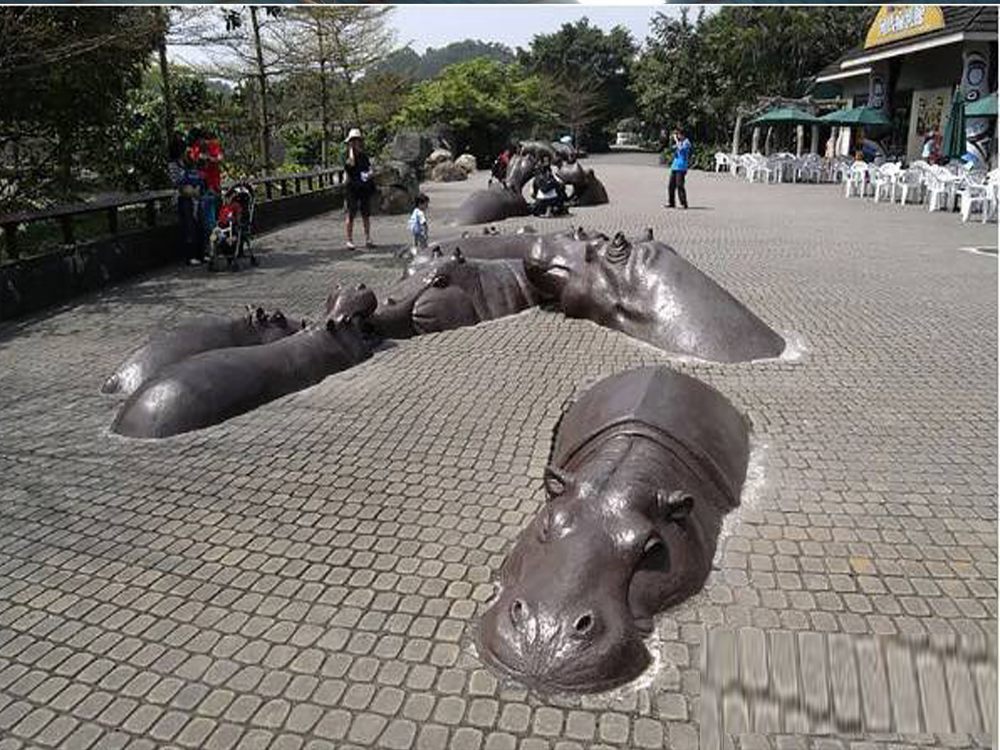
Glaze crawling, a common defect in porcelain sculptures, occurs when the glaze separates and retracts during firing, leaving bare patches. Artists and manufacturers address this issue through a combination of material science and precise craftsmanship.
1. Optimal Glaze Composition: Adjusting the glaze formula with the right balance of silica, alumina, and fluxes ensures proper melting and adhesion. Overly fluid or high-shrinkage glazes are avoided.
2. Surface Preparation: Thorough cleaning and light sanding remove dust or oils that hinder glaze bonding. Some artists apply a thin slip layer to enhance adhesion.
3. Controlled Application: Multiple thin glaze layers are preferred over a single thick coat. Dipping or spraying ensures even coverage, while brushing may cause uneven drying.
4. Kiln Mastery: Slow bisque firing burns out organic residues, while precise final firing temperatures (typically 1200-1300°C) prevent premature glaze movement. Ramp rates and cooling cycles are carefully programmed.
5. Testing Protocols: Small test tiles with identical clay/glaze combinations help predict crawling tendencies before full-scale production.
Contemporary solutions include using commercial anti-crawling additives or reformulating glazes with higher clay content. Master ceramicists often document their firing schedules to replicate success. By understanding clay-glaze interaction, creators minimize this frustrating defect, ensuring flawless porcelain artworks.