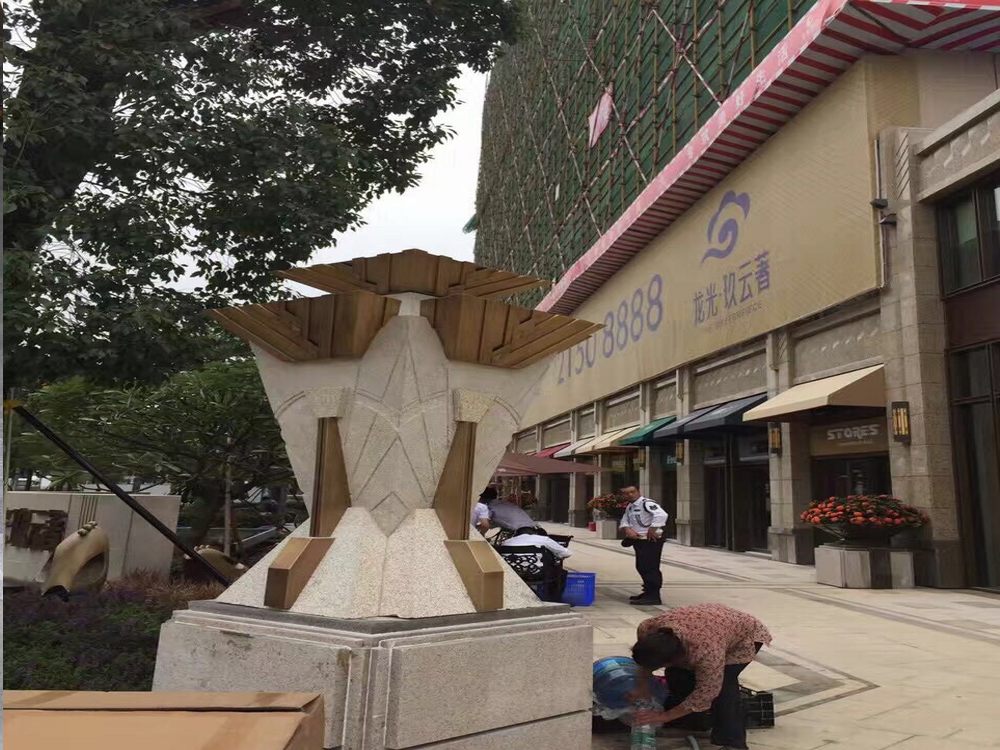
Creating porcelain sculptures with uniform colors is an alchemy of science and artistry. Seasoned ceramicists employ four key strategies to combat firing inconsistencies:
1. Precise Glaze Formulation
Artists develop proprietary glaze recipes with stable metallic oxides (like cobalt for blue or iron for amber) that react predictably across temperature ranges. Many maintain detailed glaze logs tracking chemical ratios and their chromatic outcomes.
2. Kiln Mapping Technology
Modern artists use computerized kilns with multiple thermocouples to identify hot/cold zones. By positioning sculptures strategically and programming customized firing curves (often holding at critical temperatures like 1250°C), they compensate for thermal variations.
3. Test Tile Systems
Before full-scale production, artists fire "test tiles" – small glaze samples under different conditions. The Smithsonian Archives reveal 18th-century Meissen artisans used numbered tile sets to correlate colors with specific kiln atmospheres (reduction/oxidation).
4. Post-Firing Enhancements
When minor discrepancies occur, techniques like:
- Cold painting (applying ceramic stains post-firing)
- Patina washes (iron nitrate solutions for tonal unity)
- Selective polishing (matte/gloss adjustments)
Contemporary artists like Beth Cavener employ spectral analyzers to digitize glaze colors, creating "color passports" that ensure batch-to-batch fidelity. This marriage of ancestral wisdom and modern instrumentation allows porcelain hues to remain true from studio to collector.