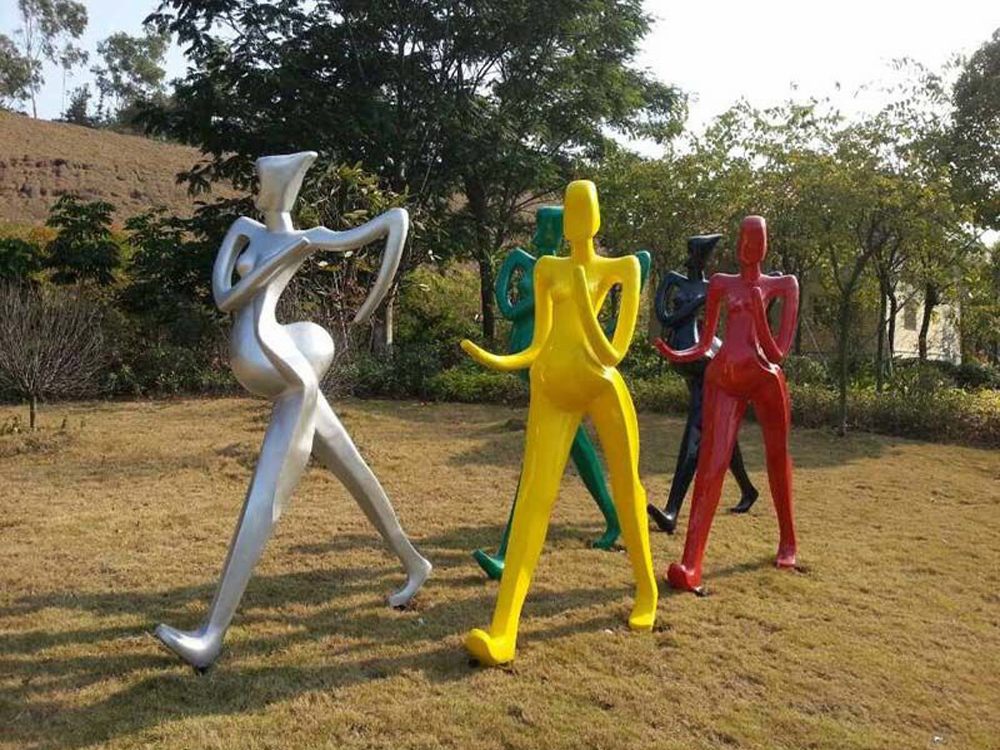
Creating porcelain sculptures with mixed glaze textures is a delicate balance of artistry and technical precision. Artists and manufacturers face several challenges, including glaze compatibility, firing temperatures, and achieving consistent results.
One major hurdle is ensuring different glazes adhere properly without cracking or peeling. Artists often layer glazes with similar thermal expansion rates or use intermediary coatings to prevent separation. Manufacturers may test hundreds of glaze combinations before finding the perfect blend.
Firing presents another challenge. Mixed glazes often require precise kiln temperatures, as some compounds mature at different heat levels. Many studios now use computerized kilns with multi-stage firing programs to accommodate diverse glaze needs.
Texture consistency is equally crucial. Artists employ techniques like wax resist or masking to control glaze application, while manufacturers might use spray guns for even coverage. Some creators even hand-paint intricate details after the initial firing.
Innovative solutions continue to emerge, from nano-glaze technologies to 3D-printed porcelain forms designed specifically for complex glaze applications. These advancements help preserve porcelain's timeless beauty while pushing artistic boundaries.
Ultimately, successful mixed-glaze porcelain sculptures represent a harmonious marriage of centuries-old ceramic traditions with modern material science, showcasing human creativity's ability to overcome technical limitations.