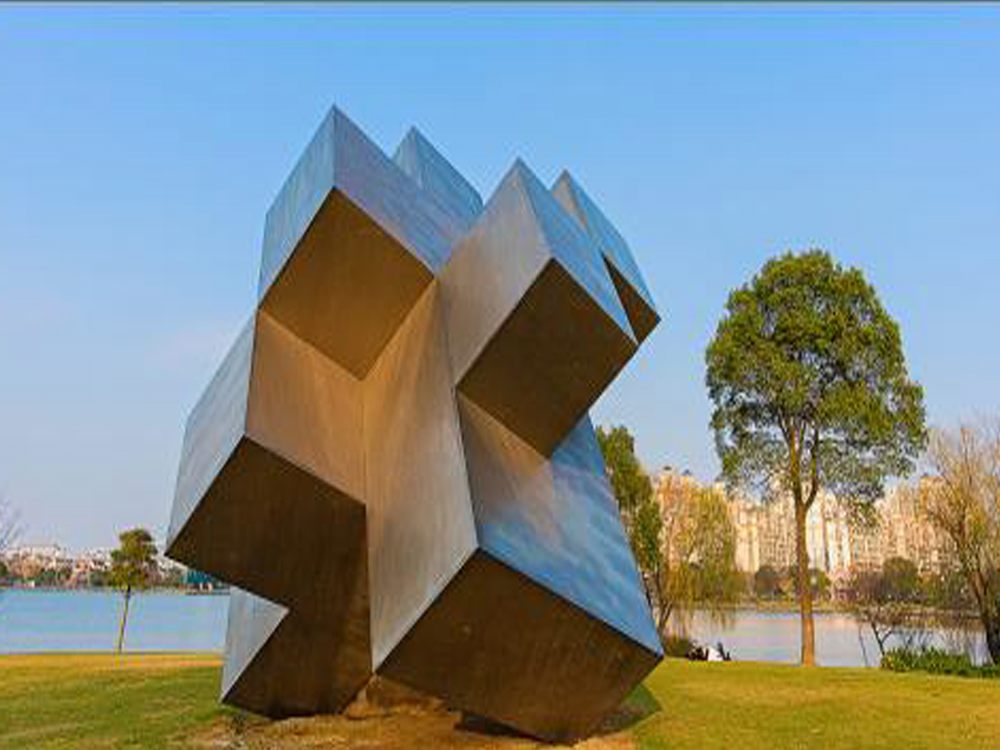
Creating porcelain sculptures with kinetic elements is a fascinating yet demanding artistic endeavor that blends delicate craftsmanship with mechanical ingenuity. One of the primary challenges lies in porcelain's inherent fragility—its brittle nature makes it susceptible to cracking or breaking when subjected to movement or stress. Artists must carefully engineer joints and moving parts to accommodate motion while preserving structural integrity.
Another hurdle is the material's sensitivity to temperature changes during firing. Kinetic components often require precise tolerances, but porcelain shrinks unpredictably in the kiln, potentially disrupting carefully planned mechanisms. This demands meticulous calculations and multiple test firings to achieve functional results.
The integration of non-ceramic components like metal axles or bearings introduces further complexity. These materials expand and contract differently from porcelain when heated, risking cracks or misalignment. Artists must either design around these limitations or develop innovative hybrid firing techniques.
Weight distribution presents yet another obstacle. Porcelain's density can make moving parts top-heavy, requiring counterbalancing solutions that don't compromise the sculpture's aesthetic harmony. Many artists address this by hollowing components or using lightweight materials for certain elements.
Despite these challenges, successful kinetic porcelain sculptures achieve a magical quality—their ethereal beauty combined with subtle motion creates artworks that seem to breathe with life. The technical difficulties only heighten their artistic value when mastered, representing a remarkable fusion of ceramic tradition and mechanical innovation.