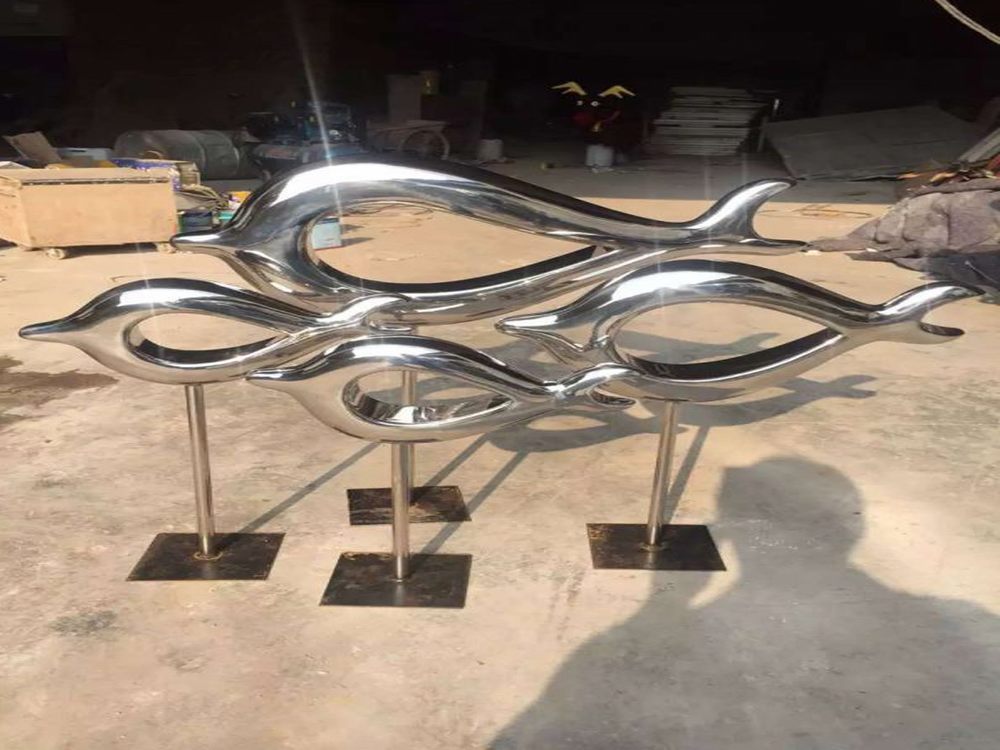
Porcelain sculptures captivate viewers with their ethereal beauty, particularly when artists masterfully incorporate translucent effects. Achieving this delicate quality requires a combination of specialized techniques and material expertise.
Artists primarily rely on ultra-thin porcelain construction, carefully controlling clay thickness to allow light penetration. The finest Chinese porcelain clay, known for its purity and whiteness, serves as the ideal base material. Skilled ceramists employ precise wheel-throwing or slip-casting methods to create paper-thin sections, sometimes as slim as 1-2 millimeters.
Firing techniques play a crucial role in developing translucency. Artists use high-temperature kilns (1280-1400°C) to vitrify the clay completely, creating a dense yet light-permeable structure. Multiple firings with specialized glazes can enhance this effect, though each firing risks warping or cracking the delicate pieces.
However, significant limitations constrain this artistic pursuit. Structural integrity becomes problematic with extremely thin walls, limiting sculpture size and complexity. The firing process remains unpredictable - thermal shock may cause catastrophic failure of thin sections. Additionally, achieving uniform translucency across large surfaces proves exceptionally difficult, often restricting artists to smaller works or partial translucent effects.
Modern artists sometimes incorporate LED lighting systems to enhance the translucent illusion, though purists argue this deviates from traditional ceramic artistry. As porcelain technology advances, some contemporary ceramists experiment with nano-porous materials and computer-aided design to push these boundaries further, yet the fundamental limitations of clay physics continue to define this exquisite art form's possibilities.