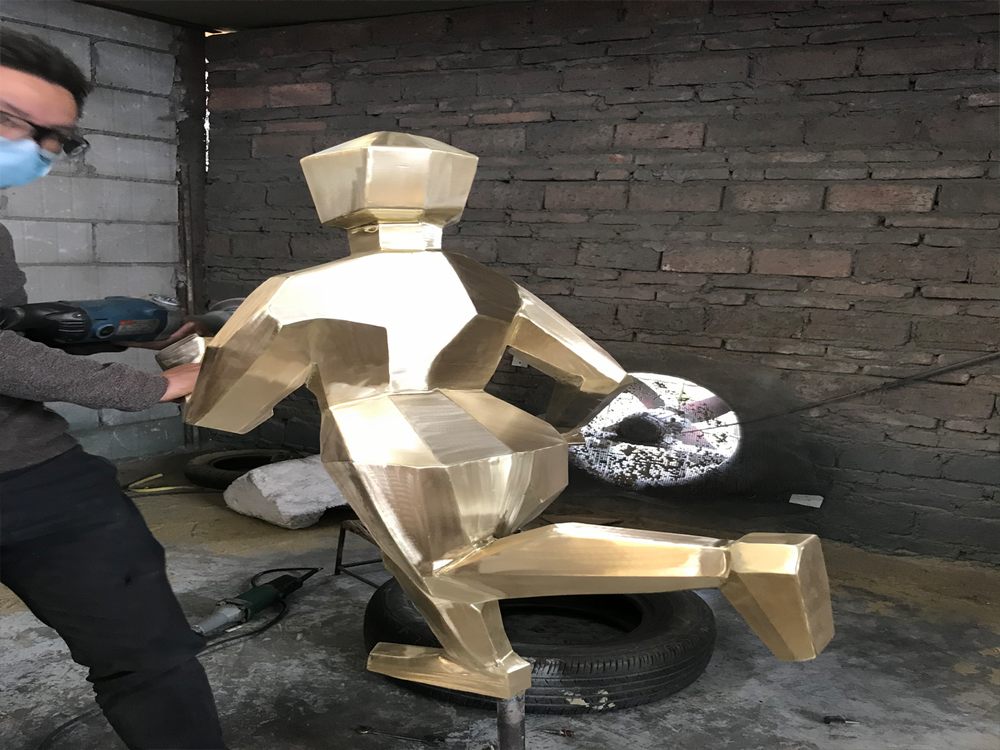
Glaze compatibility with clay bodies is a critical challenge in ceramics, requiring careful consideration of thermal expansion, chemistry, and application techniques. Artists and manufacturers address this issue through several methods:
1. Testing and Experimentation: Small test tiles are created to observe how glazes interact with specific clay bodies under firing conditions, adjusting recipes as needed.
2. Matching Thermal Expansion: Glazes must expand and contract at similar rates to the clay to prevent cracking. Manufacturers often formulate glazes tailored to common clay types.
3. Layering Techniques: Artists may apply intermediary slips or engobes to bridge differences between clay and glaze, improving adhesion and finish.
4. Controlled Firing Schedules: Adjusting kiln temperature ramps and cooling rates helps mitigate stress between glaze and clay, reducing defects like crazing or shivering.
5. Specialized Glaze Formulations: Some manufacturers produce "universal" glazes designed to work across multiple clay bodies, simplifying the process for potters.
By combining scientific understanding with artistic intuition, ceramicists achieve stunning, durable results regardless of clay-glaze pairings.