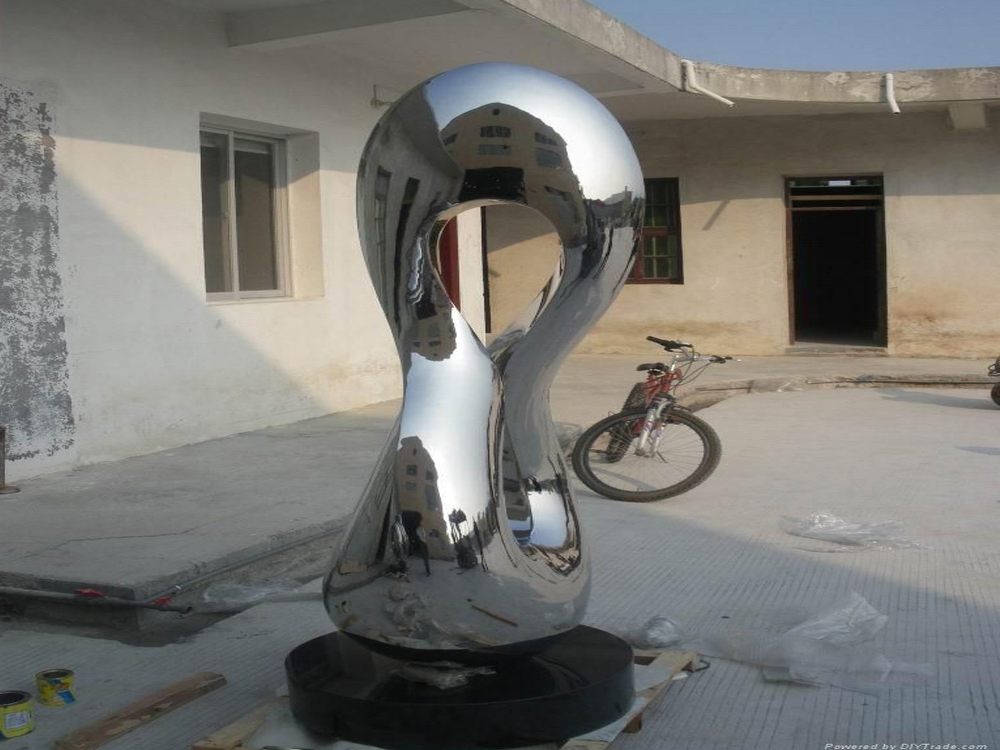
Porcelain artists face a significant challenge during the drying and firing stages: shrinkage. As clay loses moisture and undergoes high-temperature firing, it contracts, often leading to cracks or deformities. To address this, skilled ceramists employ several strategies.
First, they carefully control the drying process by wrapping pieces in plastic or using damp boxes to slow moisture evaporation, ensuring even contraction. Wedging clay thoroughly removes air pockets that could cause uneven shrinkage. Many artists also mix grog (pre-fired clay particles) into their clay body to reduce overall shrinkage rates.
During firing, a gradual temperature increase is critical. Artists often bisque-fire pieces at lower temperatures before the final glaze firing, allowing the clay to stabilize. Kiln schedules are meticulously planned, with slow heating and cooling cycles to minimize stress on the material.
Some ceramists compensate for shrinkage by making pieces slightly larger than needed, calculating the expected contraction based on their specific clay body's properties. Advanced techniques include using computer modeling to predict shrinkage patterns or creating custom clay formulations with controlled shrinkage rates.
Through these methods, artists transform porcelain's natural vulnerability into predictable, manageable characteristics, ensuring their delicate creations emerge from the kiln intact and beautiful.