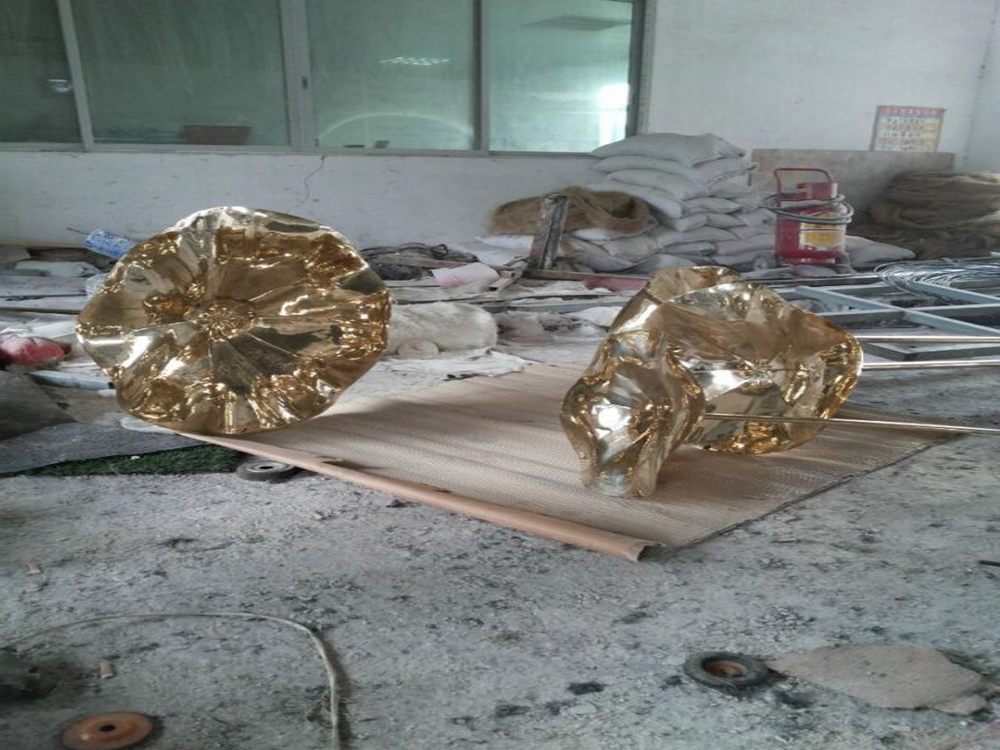
Creating porcelain sculptures with extreme thinness is a breathtaking yet demanding art form that pushes the boundaries of ceramic craftsmanship. One of the most significant challenges lies in the material's inherent fragility—porcelain becomes increasingly delicate as walls thin, making every stage from shaping to handling perilous. Master artisans must develop an extraordinary touch to manipulate the clay without causing tears or warping, often working with walls barely thicker than a sheet of paper.
The drying process presents another critical hurdle. Uneven moisture evaporation can lead to cracking or distortion, requiring controlled environments and patient timing. Firing thin porcelain demands precise kiln temperature management, as thermal shock can instantly destroy months of work. Many artists develop custom firing schedules, sometimes involving multiple low-temperature bisque firings before the final high-temperature glaze firing.
Structural integrity poses constant dilemmas—achieving both ethereal thinness and necessary support often requires innovative engineering solutions hidden within the sculpture's design. The translucent quality that makes thin porcelain so magical also means every imperfection becomes glaringly visible, demanding flawless execution.
Despite these challenges, contemporary artists continue innovating with specialized tools, custom clay formulas, and centuries-old techniques refined through relentless experimentation. The result? Breathtaking works that seem to defy gravity and material limitations, testaments to human patience and artistic vision.