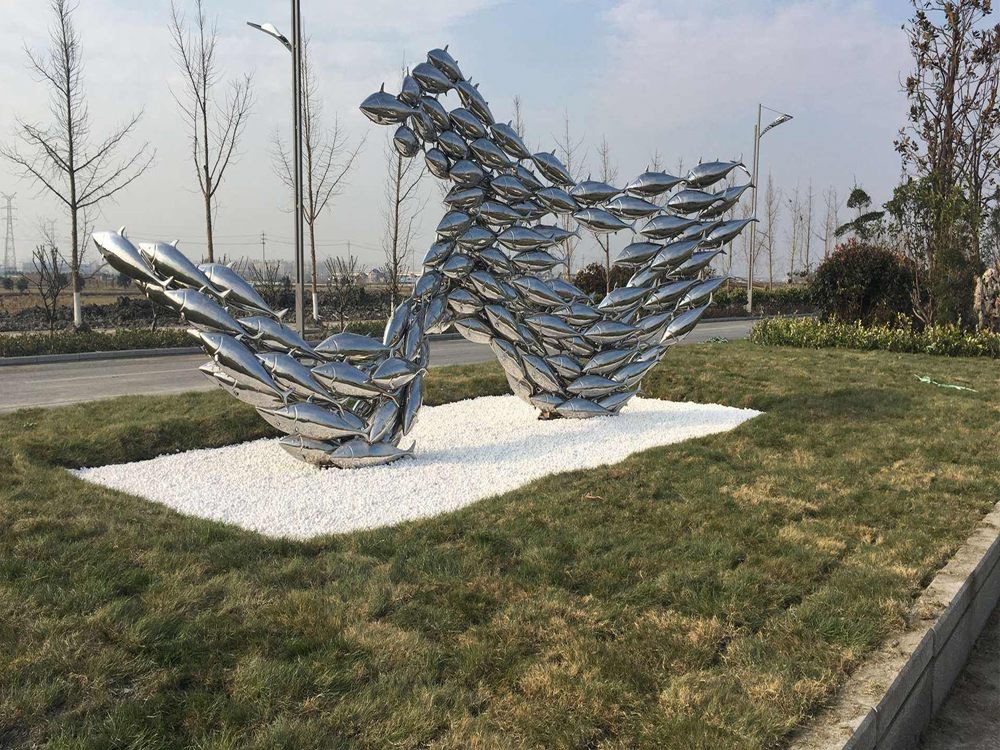
Artists working with detailed porcelain face the challenge of glaze running or pooling, which can obscure intricate designs. To address this, they employ several specialized techniques. First, precise control of kiln temperature is critical—artists often use slower firing cycles and lower peak temperatures to allow gradual glaze melting. Second, the viscosity of the glaze mixture is carefully adjusted; adding materials like alumina or silica increases thickness, reducing flow. Third, application methods matter: multiple thin layers are preferred over single thick coats, with drying time between applications.
Experienced porcelain artists also strategically plan their designs, placing detailed elements in areas less prone to pooling, such as vertical surfaces. Some even create small test pieces with identical glazes to predict behavior before committing to final works. The choice of clay body plays a role too—porcelain with higher kaolin content resists warping at high temperatures. Finally, innovative solutions like computerized kilns with programmable firing schedules and specialized stilts to elevate pieces have revolutionized precision in contemporary porcelain art. These combined approaches allow artists to maintain exquisite detail while achieving perfect glaze finishes.