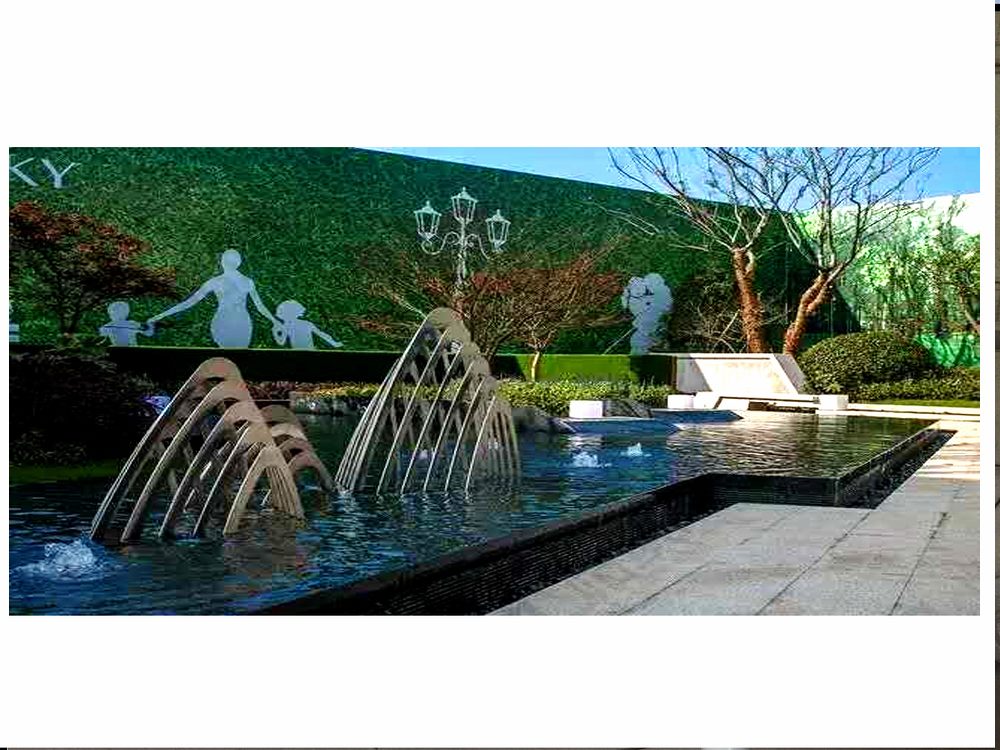
Creating porcelain sculptures with embedded aromatic elements is a delicate fusion of artistry and sensory innovation. To achieve exceptional results, begin by selecting high-quality porcelain clay, ensuring it has the right plasticity and purity for intricate detailing. The aromatic components—such as essential oils or natural resins—should be carefully chosen for their longevity and compatibility with firing temperatures.
A key technique involves embedding the fragrance into the clay body before shaping. Mix microencapsulated oils or porous ceramic pellets infused with scent into the clay, allowing even distribution. Alternatively, hollow cavities can be designed within the sculpture to hold aromatic inserts post-firing.
Firing is critical; low-temperature bisque firing (around 900°C) preserves delicate fragrances, while glazing should use non-reactive, transparent coatings to avoid scent interference. For durability, opt for slow cooling to prevent cracks.
Finally, balance aesthetics and functionality. Subtle scent diffusion enhances the viewer’s experience without overwhelming the visual appeal. This harmonious blend elevates porcelain sculptures into multisensory masterpieces.