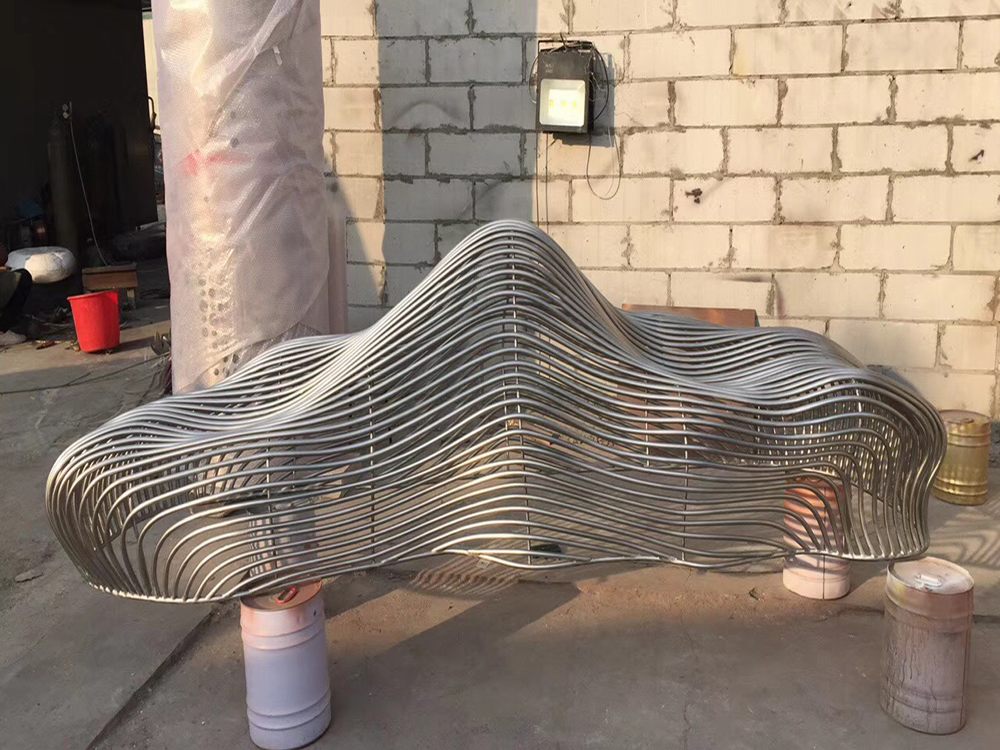
Creating porcelain sculptures with extreme height-to-width ratios is a delicate dance between artistry and engineering. The primary challenge lies in the material's inherent fragility—porcelain, while prized for its luminous beauty, lacks the tensile strength of other mediums. As the sculpture's height increases relative to its narrow base, the risk of collapse during shaping, drying, or kiln firing multiplies exponentially.
Artists must account for clay memory—the tendency of porcelain to sag under its own weight during the slow drying process. This requires innovative armature systems or temporary supports that won't compromise the final form. The firing process presents another hurdle, as thermal dynamics can cause uneven shrinkage (often 12-15%) that distorts carefully calculated proportions.
Techniques like slip-casting multiple sections or incorporating hidden structural reinforcements are often employed, but these solutions must balance structural integrity with aesthetic purity—a core value in porcelain art. The most successful works achieve an impossible-seeming balance, where gravity-defying elegance emerges from countless hours of material testing and artistic problem-solving.