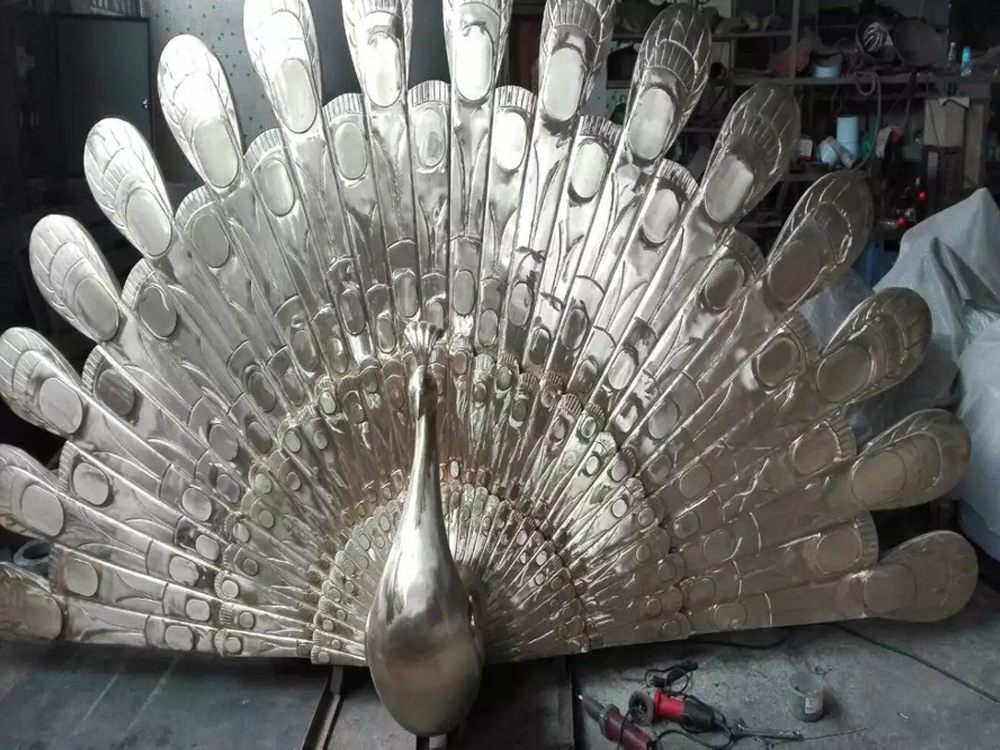
Scaling up a small porcelain sculpture design for mass production presents several unique challenges that can impact quality, cost, and efficiency. One major hurdle is maintaining material consistency. Porcelain's delicate nature requires precise control over clay composition and firing conditions, which becomes harder to manage at larger scales.
Another challenge lies in mold design. Small sculptures often have intricate details that may not transfer well to production molds, leading to loss of definition or requiring costly mold adjustments. The expansion and contraction rates of porcelain during firing also complicate dimensional accuracy when producing thousands of pieces.
Production timing introduces additional difficulties. The lengthy drying and firing cycles needed for porcelain don't easily accommodate rapid mass production schedules. Each piece must go through multiple firings (bisque, glaze, sometimes decoration firings), creating bottlenecks.
Cost factors emerge when moving from handmade to manufactured pieces. While unit costs decrease with volume, the initial investments in mold creation, kiln capacity, and quality control systems can be substantial. There's also the challenge of training workers to handle delicate unfired pieces consistently.
Finally, quality control becomes exponentially more difficult. Small variations that might be acceptable in one-off art pieces become unacceptable defects in mass production, requiring rigorous inspection processes that can slow production further.
Successful scaling requires careful planning in these areas: investing in high-quality mold technology, developing strict process controls, and sometimes simplifying designs to accommodate production realities while maintaining artistic integrity.