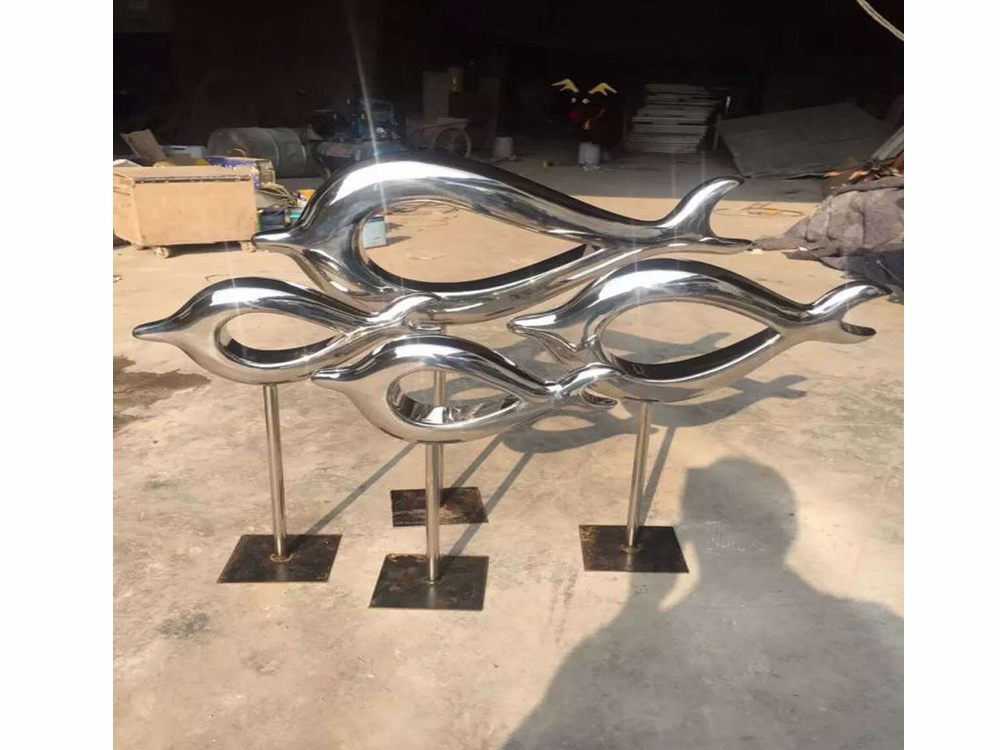
Creating porcelain sculptures with delicate, protruding elements is a demanding art form that requires precision, patience, and innovative techniques. Artists face numerous challenges, such as structural fragility, warping during firing, and maintaining intricate details. To address these issues, they employ specialized methods like slip casting for uniformity, reinforcing weak points with internal supports, and carefully controlling kiln temperatures to prevent cracks.
Many sculptors use high-quality porcelain clay with added grog for stability, while others layer thin coils or slabs to build protruding sections gradually. Advanced drying techniques, such as slow air-drying or humidity chambers, help minimize stress. Glazing demands equal attention—artists often apply multiple thin layers to avoid pooling or weakening delicate areas.
Mastering these techniques allows artists to push the boundaries of porcelain art, transforming fragile material into breathtaking sculptures that defy expectations. The result is a testament to both artistic vision and technical expertise.