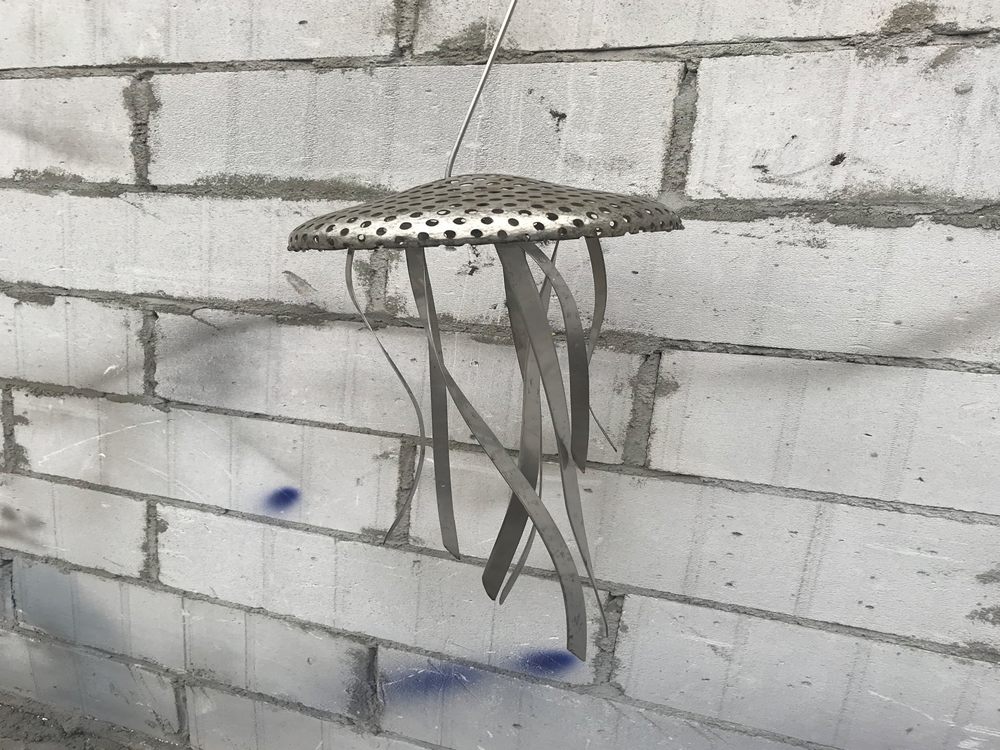
Creating porcelain sculptures with intricate, interlocking parts is a delicate art form that demands precision, patience, and innovation. Artists face numerous challenges, from ensuring structural integrity to maintaining aesthetic harmony. Here’s how they address these complexities:
1. Material Mastery: Porcelain’s fragility requires artists to understand its properties deeply. They often mix clay with additives to enhance flexibility and reduce cracking during drying and firing.
2. Modular Design: To manage interlocking parts, sculptors frequently adopt a modular approach. Each component is crafted separately, tested for fit, and then assembled before the final firing.
3. Precision Tools: Specialized tools like fine needles, micro-saws, and 3D-printed molds help achieve the exactness needed for interlocking mechanisms.
4. Controlled Drying and Firing: Uneven drying can warp parts, ruining their fit. Artists use slow-drying techniques and kilns with precise temperature controls to prevent distortion.
5. Innovative Joining Techniques: Instead of traditional adhesives, some artists use slip (liquid clay) or hidden supports to bond parts seamlessly, ensuring durability without compromising design.
6. Problem-Solving Mindset: Every sculpture presents unique challenges. Artists often prototype with cheaper materials like wax or polymer clay before committing to porcelain.
Through these methods, artists transform the limitations of porcelain into opportunities for breathtaking, intricate sculptures that captivate and inspire.