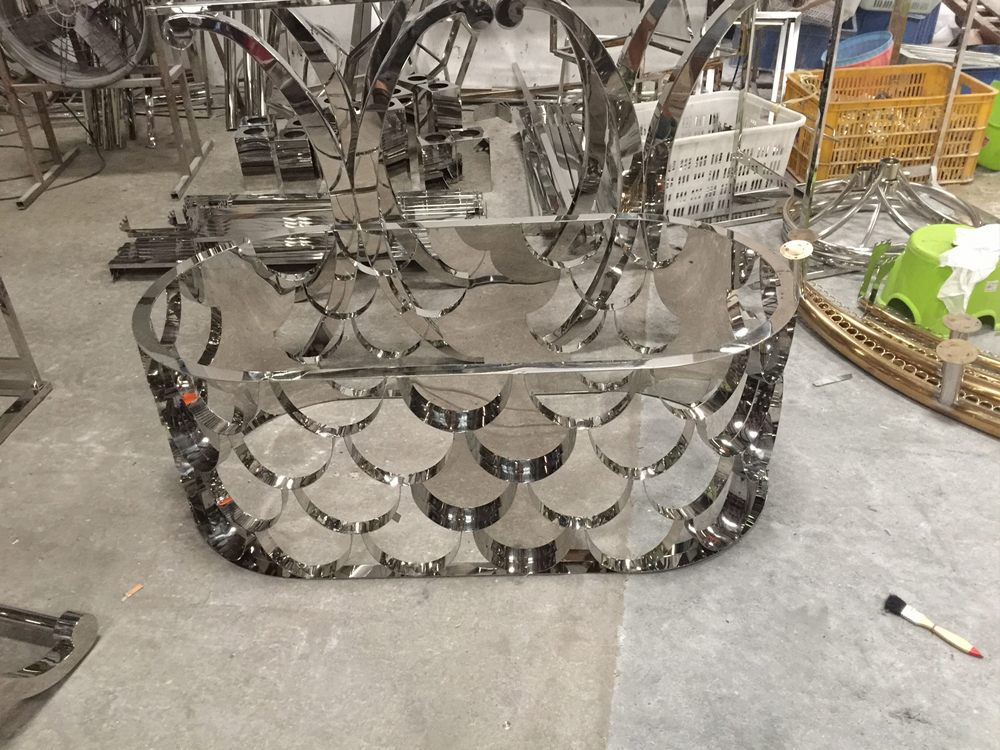
Creating exquisite porcelain sculptures requires not only artistic skill but also access to premium materials. However, sourcing high-quality materials for porcelain sculptures presents several challenges that artists and manufacturers often face.
One major challenge is finding clay with the right purity and consistency. Porcelain demands fine, white kaolin clay free from impurities, which can be scarce or expensive depending on regional availability. Variations in clay composition can lead to cracking or uneven firing, ruining intricate designs.
Another hurdle is securing reliable suppliers for specialized additives like feldspar or quartz, which affect the sculpture's durability and translucency. Global supply chain disruptions further complicate consistent access to these raw materials.
The firing process also poses difficulties. High-quality porcelain requires precise kiln temperatures, often exceeding 1,300°C. Sourcing kilns capable of maintaining such heat without fluctuations is costly, and improper firing can waste valuable materials.
Additionally, achieving consistent glaze quality is challenging. Glazes must be chemically stable to prevent discoloration or bubbling, requiring rare mineral pigments that are increasingly regulated due to environmental concerns.
Finally, the time-sensitive nature of working with porcelain adds pressure. Clay dries quickly, demanding efficient material sourcing to avoid waste. These challenges highlight why mastering porcelain sculpture requires both artistic vision and meticulous material management.