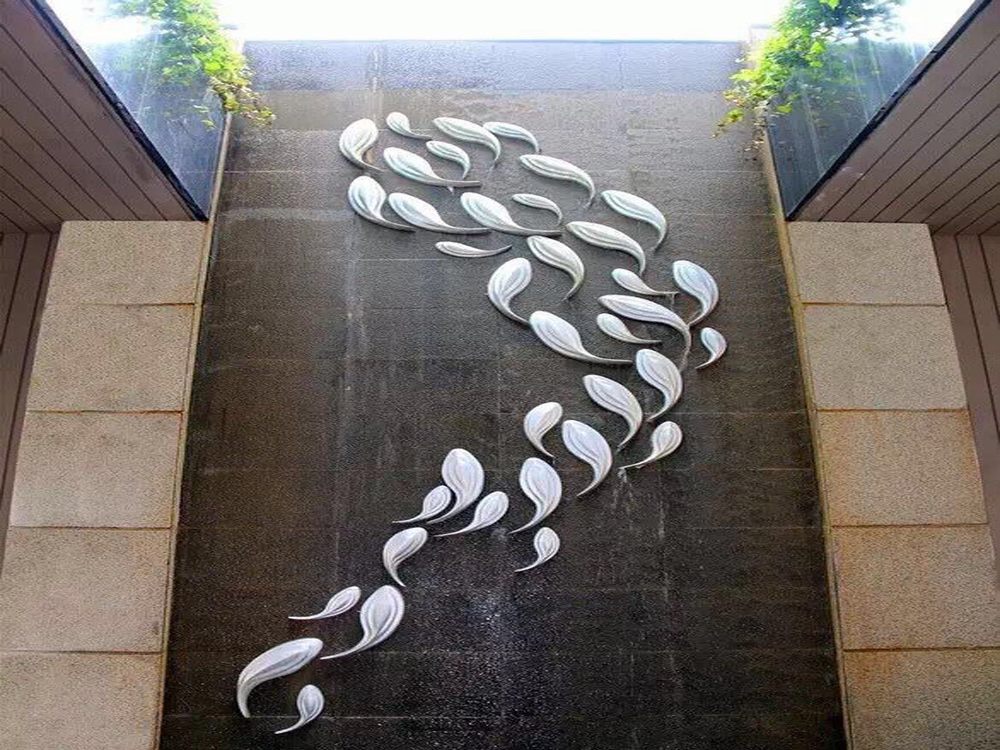
Creating porcelain sculptures with delicate, freestanding elements is a demanding art form that tests even the most skilled ceramic artists. One of the primary challenges lies in achieving structural integrity. Thin, intricate components must support their own weight while resisting breakage during both the creation process and handling. Artists often struggle with warping during drying, as uneven shrinkage can distort fragile elements.
The firing process presents another major hurdle. Porcelain's high firing temperature (often exceeding 1300°C) increases the risk of collapse or cracking, particularly for unsupported projections. Thermal shock during cooling can cause catastrophic failures in thin sections. Many sculptors combat this by designing internal support structures that burn away during firing.
Surface tension also poses unique difficulties. Unlike thicker pottery, delicate porcelain elements may bend or droop under their own weight when wet. Artists frequently employ specialized drying techniques, sometimes supporting pieces with foam or fabric until the clay reaches leather-hard consistency.
Color consistency challenges emerge when working with delicate pieces. Thin sections absorb glazes differently than thicker areas, potentially creating uneven finishes. Some artists apply multiple thin layers or use spray application methods to achieve uniform coverage without over-saturating fragile elements.
Finally, the fragility of finished pieces creates transportation and display challenges. Many sculptors develop custom packaging solutions or design sculptures with discreet reinforcement points. Despite these obstacles, mastering these techniques allows artists to create breathtaking works that seem to defy gravity and material limitations.