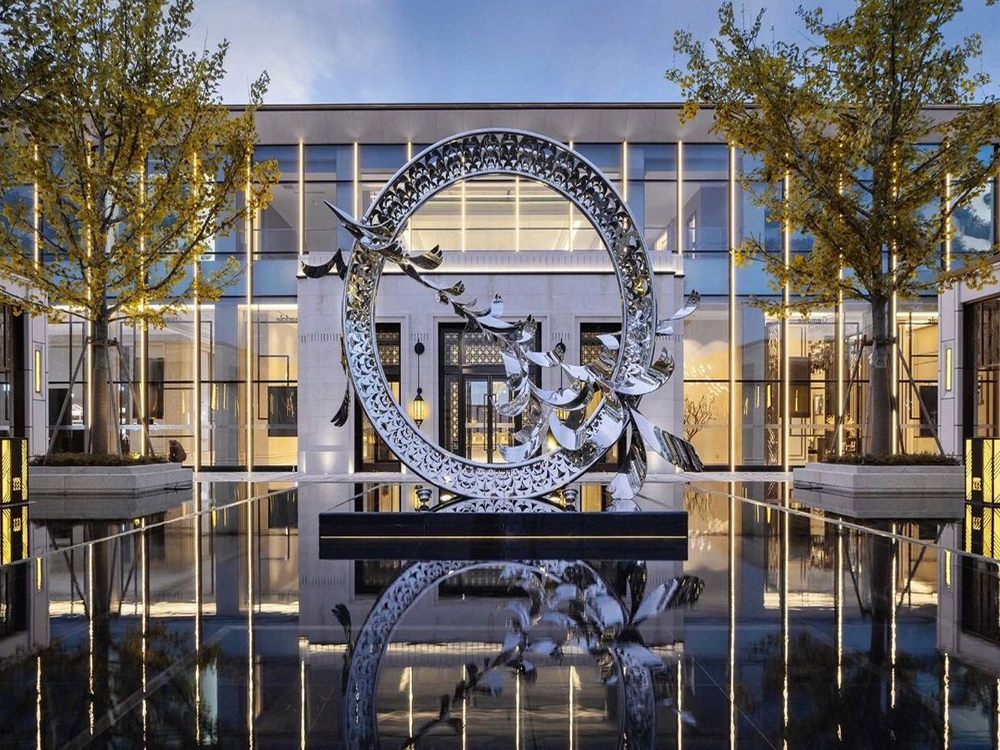
Creating porcelain sculptures requires meticulous attention to detail, especially during the drying and firing stages where cracking and warping can ruin hours of work. Artists employ several proven techniques to ensure their delicate pieces remain intact.
1. Slow and Even Drying: Rapid drying is a primary cause of cracks. Artists often cover sculptures with plastic or damp cloths to control moisture loss, allowing the piece to dry uniformly over days or weeks.
2. Proper Clay Preparation: Wedging clay thoroughly removes air bubbles, while using high-quality porcelain with balanced plasticity reduces shrinkage stress. Some artists mix grog (fired clay particles) to enhance structural stability.
3. Supportive Armatures: For complex shapes, internal supports or removable foam structures prevent sagging during drying. Hollow constructions with even wall thickness also minimize tension.
4. Controlled Kiln Firing: A slow bisque firing (under 1000°C) drives out residual water without thermal shock. Glaze firing follows a carefully ramped temperature curve, often with a "soak" period to relieve stresses.
5. Post-Firing Care: Cooling the kiln gradually prevents sudden contraction cracks. Some artists use kiln wash or stilts to avoid glaze adhesion issues that could strain the sculpture.
By mastering these methods, ceramic artists transform fragile clay into enduring porcelain masterpieces, balancing chemistry, physics, and artistic vision.