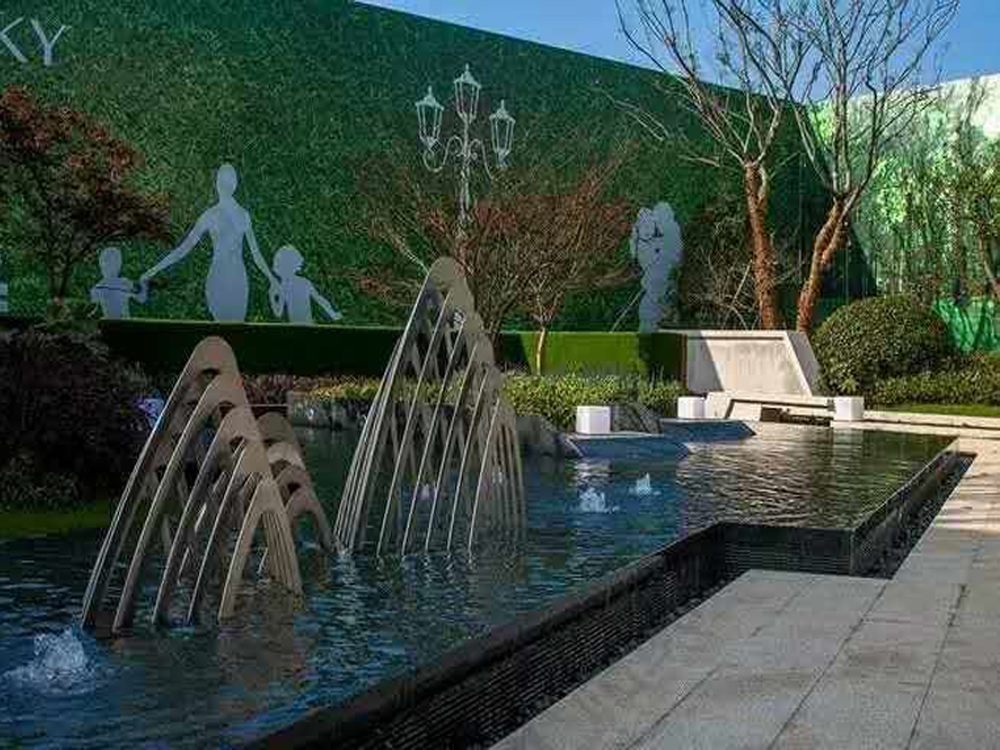
Creating multi-part porcelain sculptures is a delicate art that demands precision and expertise. One of the most common challenges is material shrinkage during the firing process. Porcelain clay contracts significantly in the kiln, often leading to misaligned joints or uneven fits between components. Artists must account for this shrinkage by carefully calculating proportions before firing.
Another hurdle is achieving seamless joins between individual pieces. Even minor imperfections in the sculpting or drying stages can result in visible gaps or weak connections. Skilled ceramists often use specialized techniques like slip casting or scoring to enhance adhesion, but these methods require meticulous execution.
The complexity of design also plays a role. Intricate sculptures with multiple interlocking parts demand flawless planning to ensure all components align perfectly post-firing. Temperature variations in the kiln can further complicate this, as uneven heat distribution may cause warping or distortion.
Finally, the fragility of porcelain adds another layer of difficulty. Handling unfired or bisque-fired pieces requires extreme care to avoid cracks or breaks that could ruin the final assembly. Mastering these challenges is what separates exceptional porcelain artists from the rest, turning functional craftsmanship into breathtaking art.