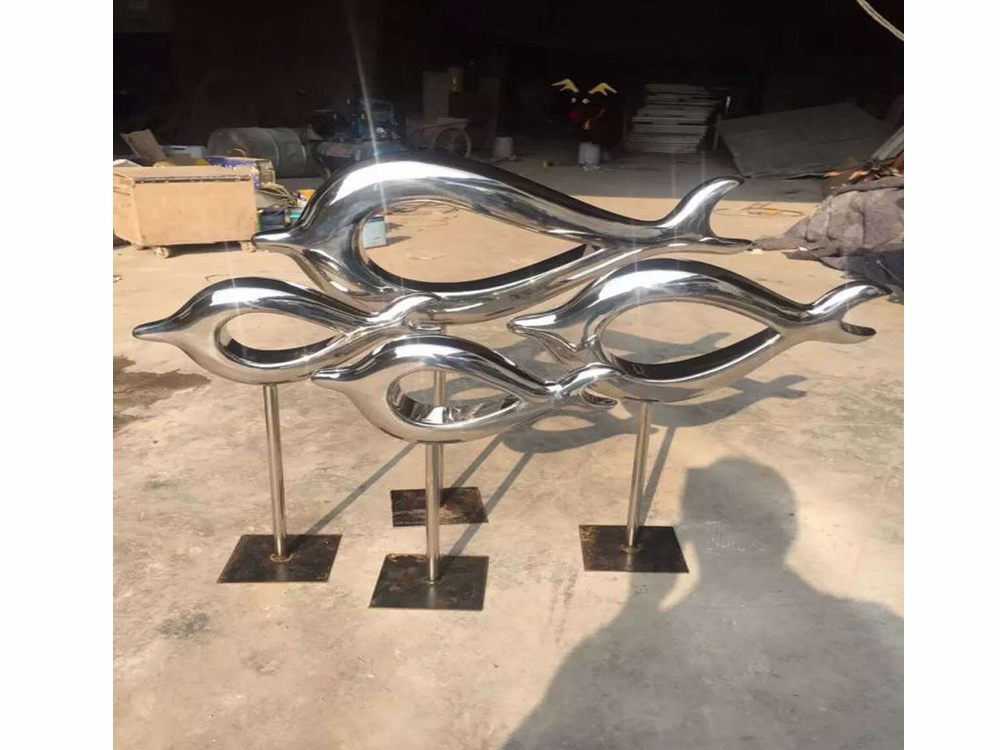
Creating a series of porcelain sculptures with uniform texture is a complex task that demands precision and expertise. One of the primary challenges is maintaining consistent clay composition, as slight variations in moisture or additives can alter the final texture. Additionally, uneven drying rates may cause cracks or warping, disrupting surface uniformity. Firing conditions also play a critical role; temperature fluctuations in the kiln can lead to inconsistent glaze results or texture deviations. Another hurdle is the artist's technique—hand-building methods like coiling or slab construction may introduce unintentional textural differences. Finally, glaze application inconsistencies, such as uneven thickness or chemical reactions, can further complicate achieving homogeneity. Mastering these variables requires meticulous attention to material selection, process control, and artistic execution.