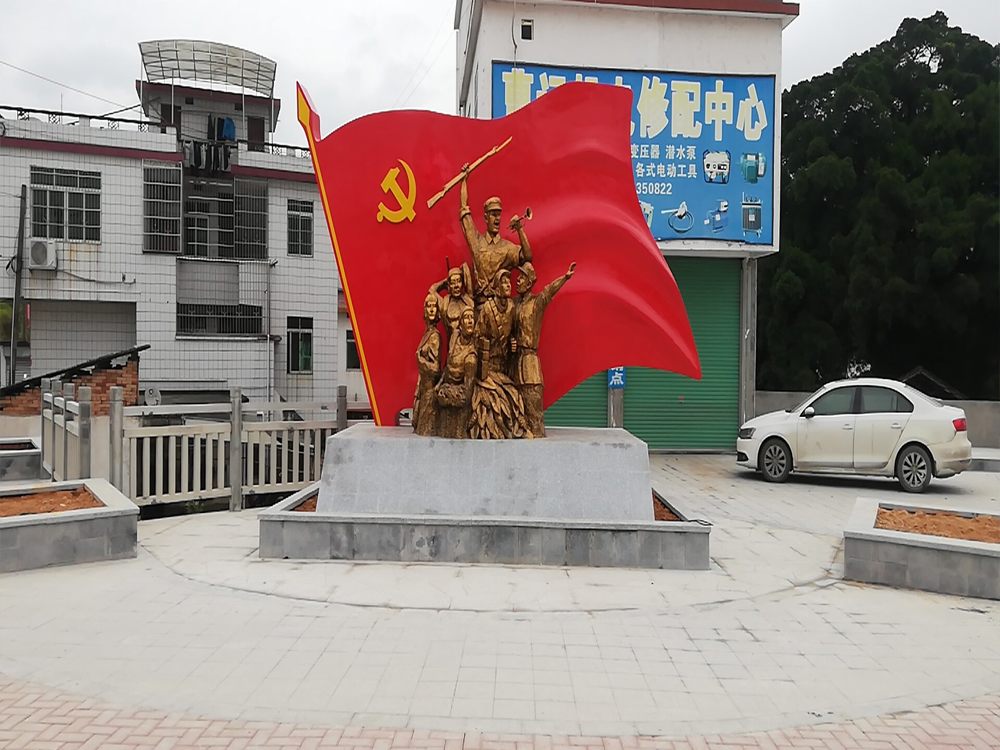
Replicating antique porcelain sculptures requires a meticulous blend of historical knowledge, artistic skill, and technical precision. Artisans begin by studying the original piece, analyzing its composition, glaze, and decorative motifs. Traditional techniques, such as hand-molding and slip casting, are often employed to recreate the form, while modern tools like 3D scanning may assist in capturing intricate details.
Glazing and firing processes are carefully matched to historical methods, with artisans sometimes using period-specific kilns or replicating vintage glaze formulas. For restoration, missing fragments are reconstructed using compatible materials, then seamlessly integrated through delicate retouching. The final step often involves artificial aging to mimic the patina of time, ensuring the reproduction or restored piece harmonizes with its antique counterpart.
Mastering these techniques demands years of apprenticeship, as artisans must understand both the material science of porcelain and the artistic styles of different historical periods. This painstaking process preserves cultural heritage while allowing collectors and museums to maintain or replace fragile antique pieces.