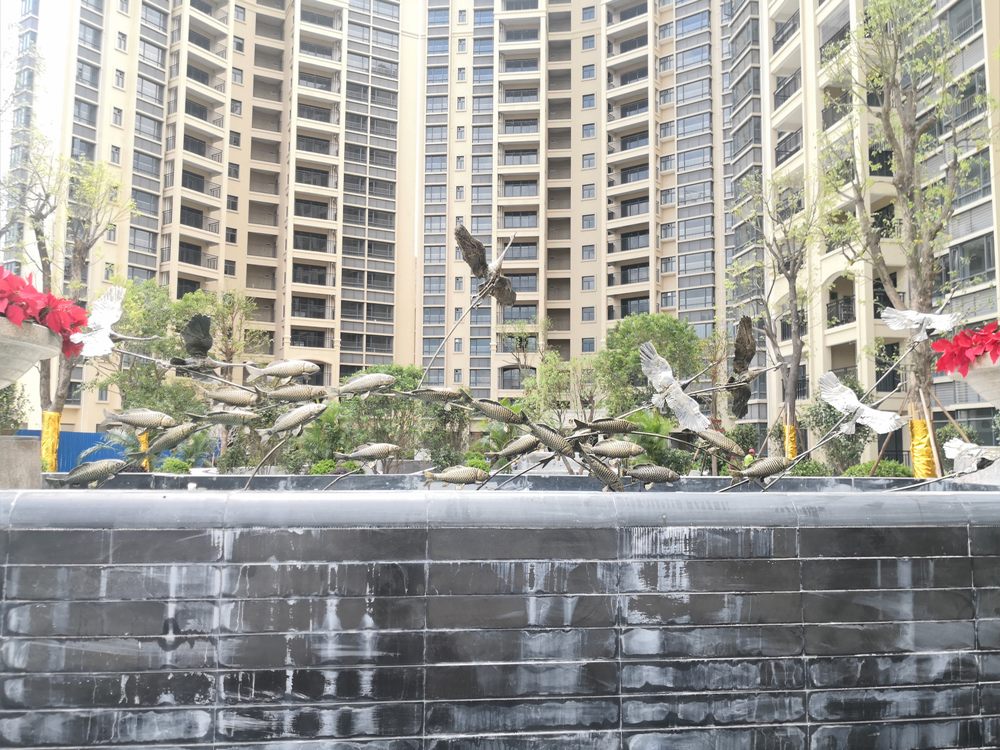
The art of porcelain sculpture has been revolutionized by modern kiln technology, which significantly enhances production efficiency while maintaining artistic integrity. Advanced kilns now feature precise temperature control systems, allowing artisans to achieve consistent results with minimal waste. Innovations like programmable firing cycles and energy-efficient designs reduce operational costs by up to 40%, while rapid heating and cooling capabilities shorten production timelines.
Contemporary kilns incorporate smart monitoring systems that track humidity, airflow, and thermal distribution in real-time, preventing cracks and deformations in delicate sculptures. Gas-fired and electric hybrid models offer cleaner firing processes with reduced environmental impact. These technological leaps enable artists to experiment with complex designs and larger formats previously impossible with traditional kilns.
The integration of AI-assisted temperature regulation and automated loading systems further optimizes workflow, allowing studios to increase output without compromising quality. As kiln technology continues evolving, porcelain sculptors gain unprecedented creative freedom while achieving remarkable production efficiencies that bridge ancient craftsmanship with modern manufacturing principles.