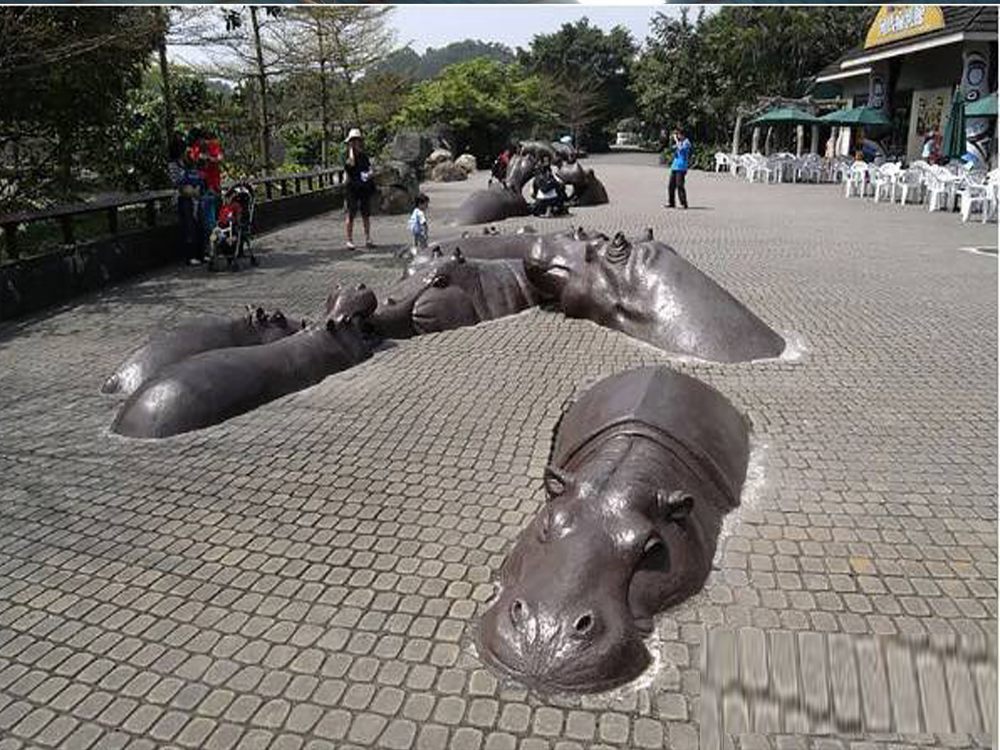
Creating porcelain sculptures with kinetic or mechanical components presents a unique set of challenges that blend artistry with engineering. One major hurdle is the inherent fragility of porcelain, which complicates the integration of moving parts. Unlike metals or plastics, porcelain lacks flexibility, making it prone to cracking under stress or repeated motion.
Another challenge lies in achieving precise mechanical functionality while maintaining aesthetic integrity. Artists must balance intricate ceramic craftsmanship with the technical demands of gears, hinges, or motors. This often requires collaboration between ceramicists and engineers, a fusion of disciplines that can be difficult to coordinate.
Temperature sensitivity also poses a problem. Porcelain undergoes high-fired kiln processes, which can warp or damage pre-installed mechanical elements. Artists must either design components to withstand extreme heat or find ways to incorporate them post-firing, adding complexity to the workflow.
Lastly, long-term durability is a concern. Porcelain’s brittleness and the wear-and-tear of moving parts raise questions about the sculpture’s lifespan. Innovations in material science and engineering are gradually addressing these issues, but the intersection of delicate ceramics and mechanics remains a frontier in sculptural art.