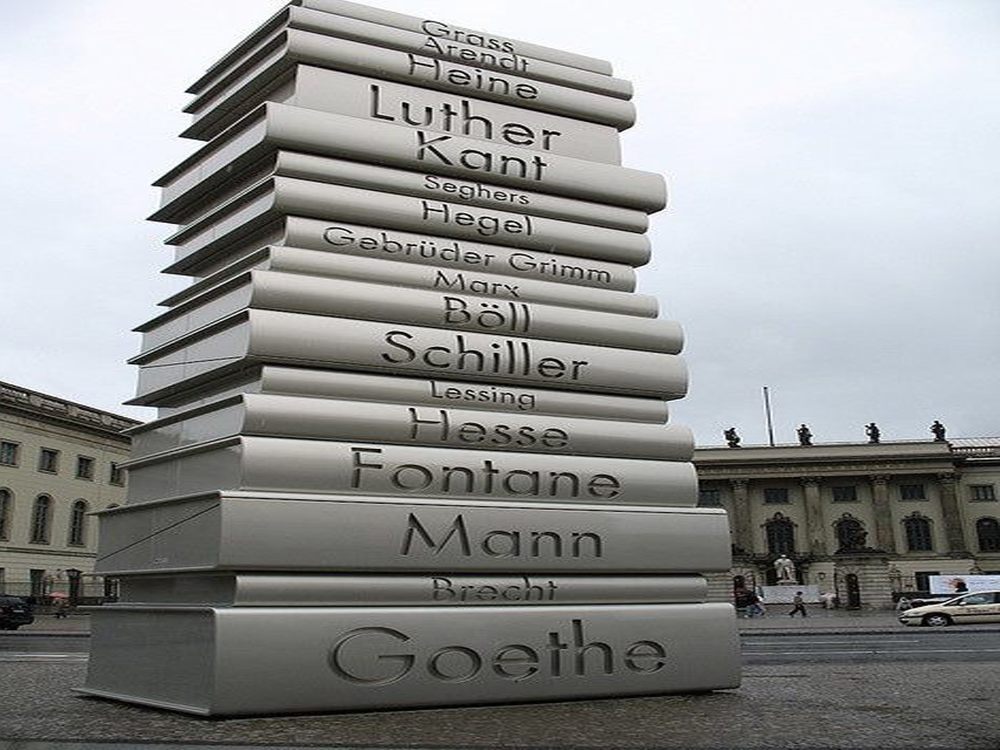
Achieving consistent results in layered glaze applications for porcelain sculptures requires a combination of meticulous preparation, precise technique, and controlled firing. Here are the most effective methods to ensure flawless outcomes:
1. Surface Preparation: Begin with a perfectly smooth bisque-fired surface. Any imperfections will magnify under multiple glaze layers. Lightly sand and clean the sculpture to remove dust.
2. Glaze Consistency: Mix glazes to a uniform, cream-like thickness. Test each layer on sample tiles to verify color and texture compatibility before applying to your sculpture.
3. Layering Technique: Apply thin, even coats using a soft brush or spray gun, allowing each layer to dry completely before adding the next. Overlapping should be minimal to prevent cracking or bubbling.
4. Controlled Drying: Slow drying between layers prevents moisture trapping, which can cause cracks. Use a humidity-controlled environment or a heat gun on low settings.
5. Firing Protocol: Program your kiln with a gradual ramp-up and cooling cycle. Sudden temperature changes may cause glaze defects. Consider test-firing small sections to refine the schedule.
6. Documentation: Keep detailed notes on glaze combinations, application thickness, and firing results. This creates a reproducible process for future projects.
By mastering these steps, artists can achieve predictable, vibrant layered glaze effects that elevate their porcelain sculptures to professional standards. Consistency comes from patience, practice, and attention to every detail in the process.