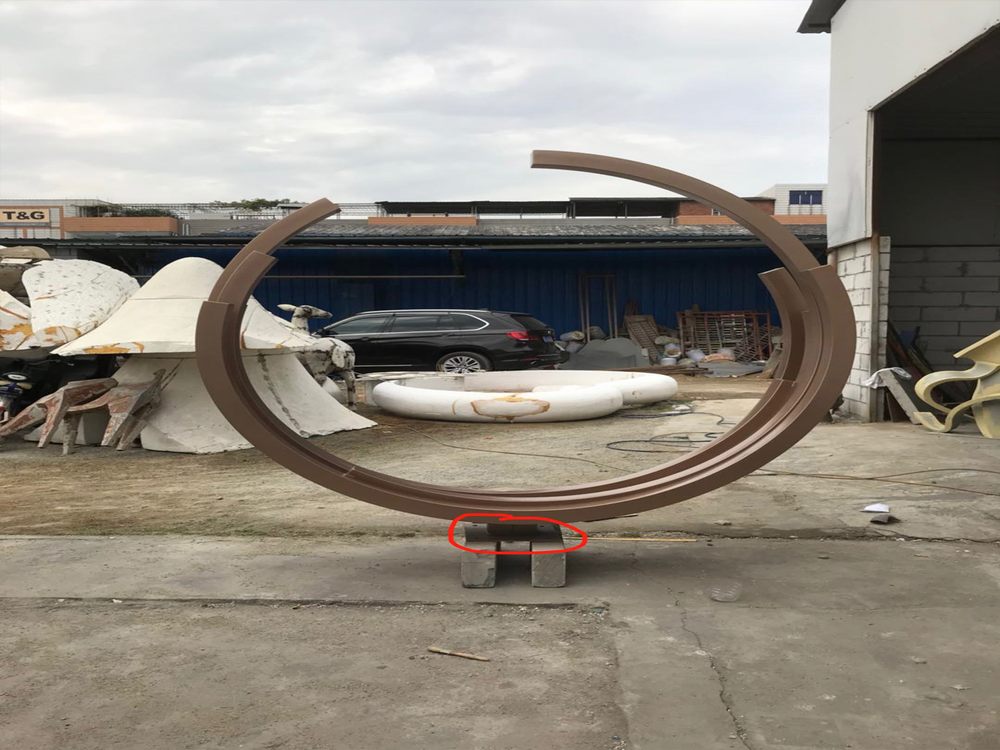
Creating porcelain sculptures with moving parts is a remarkable feat that blends artistry with engineering. However, this delicate process presents several significant challenges.
First, porcelain’s inherent fragility makes it difficult to craft functional moving components. Unlike metals or plastics, porcelain lacks flexibility, increasing the risk of cracks or breaks during assembly or movement. Artists must meticulously design joints and hinges to minimize stress on the material.
Second, the firing process introduces unpredictability. Porcelain shrinks and warps during kiln firing, which can misalign moving parts. Achieving precise tolerances requires multiple test firings and adjustments, adding time and complexity to the process.
Third, balancing aesthetics with functionality is demanding. Artists must ensure that mechanical elements like hinges or pivots remain discreet while maintaining the sculpture’s visual harmony. This often involves custom solutions, as standard hardware may disrupt the piece’s elegance.
Lastly, durability is a persistent concern. Even after successful creation, repeated movement can wear down porcelain over time. Artists often apply protective coatings or limit motion to preserve the sculpture’s longevity.
Despite these challenges, the fusion of porcelain’s beauty with kinetic elements continues to inspire innovative ceramic artists worldwide.