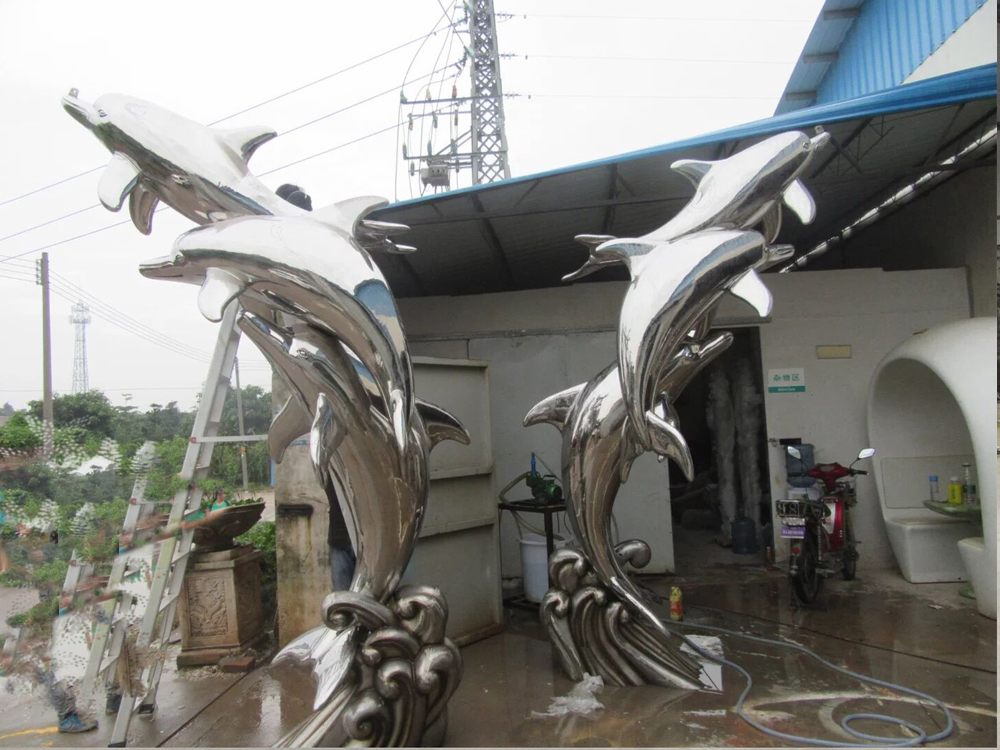
Glaze blistering, a common defect in porcelain sculptures, occurs when trapped gases or improper firing cause bubbles or cracks in the glaze surface. Artists and manufacturers employ several strategies to address this challenge:
1. Material Selection: Using high-quality clay with consistent particle size reduces impurities that can release gases during firing. Many artisans mix kaolin with other clays to enhance stability.
2. Controlled Drying: Slow, even drying prevents moisture retention that leads to blistering. Some studios use humidity-controlled rooms for large pieces.
3. Bisque Firing Optimization: A properly executed bisque firing (typically 900-1000°C) burns out organic materials before glazing. Manufacturers often program computerized kilns with gradual temperature ramps.
4. Glaze Chemistry: Experienced ceramists adjust glaze formulations to match the clay body's expansion rate. Adding silica or alumina can increase viscosity, reducing bubble formation.
5. Kiln Atmosphere Control: Oxidation versus reduction firing significantly affects glaze outcomes. Many contemporary artists use electric kilns with precise atmosphere controls for delicate pieces.
6. Multiple Firing Techniques: Some porcelain artists employ low-temperature glaze firings followed by higher final firings to minimize defects.
7. Cooling Rate Management: Controlled cooling cycles (especially between 800-500°C) prevent thermal shock that can cause micro-blistering.
Advanced workshops now utilize digital pyrometers and thermal imaging to monitor heat distribution, while traditional artisans rely on centuries-old observation techniques like cone packs and spy holes. The most successful solutions combine scientific understanding with artistic intuition, ensuring both aesthetic quality and structural integrity in finished porcelain works.