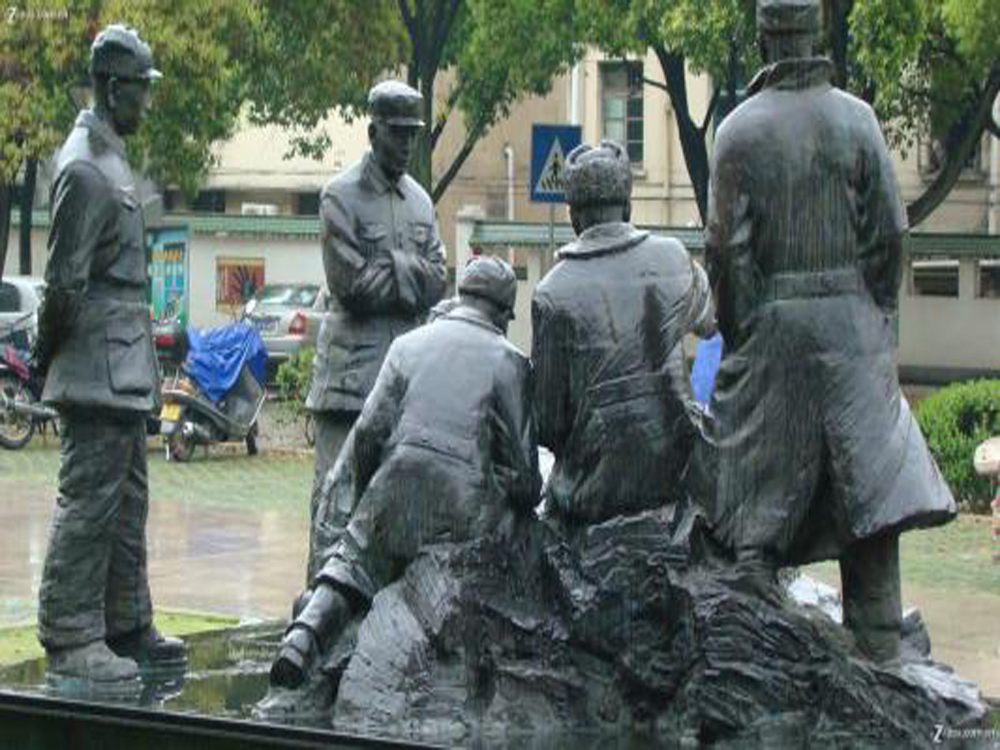
The choice of kiln—whether electric, gas, or wood-fired—plays a crucial role in determining the final quality of porcelain sculptures. Each type of kiln offers distinct advantages and challenges that impact texture, color, and durability.
Electric kilns provide precise temperature control, making them ideal for consistent glazing and uniform heating. However, they may lack the atmospheric richness that gas or wood-fired kilns offer. Gas kilns, on the other hand, allow for reduction firing, which can create unique metallic and crystalline effects on porcelain surfaces. The controlled yet dynamic environment of a gas kiln enhances depth in glazes.
Wood-fired kilns introduce natural ash deposits and unpredictable flame patterns, resulting in organic, one-of-a-kind finishes. The extended firing process in wood kilns can also strengthen porcelain, though it requires expert handling to avoid cracking.
Ultimately, the kiln type shapes the artistic expression and structural integrity of porcelain sculptures. Artists must weigh consistency against spontaneity when selecting the best firing method for their work.